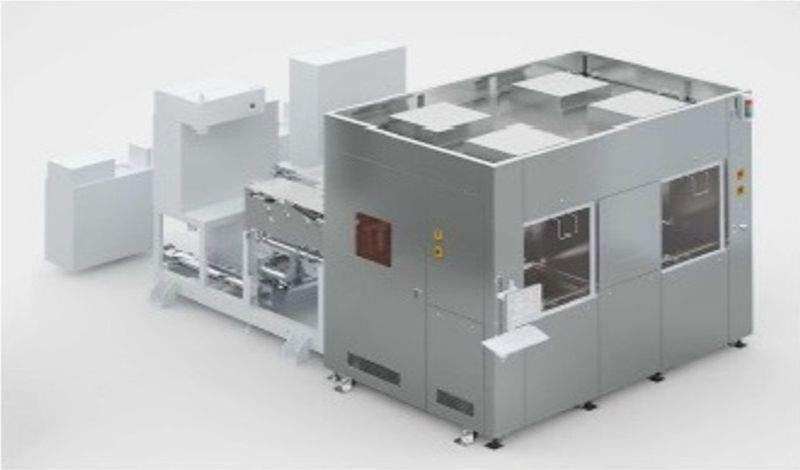
Japan-based Ulvac has developed a new dry etching system, NA-1500, for 600mm advanced packaging substrates.
Designed to provide a uniform descum process for a large square substrate, the new system will enable packaging manufacturers to reduce their fan-out wafer level package (FO-WLP) costs.
In recent times, packaging manufacturers have also increased their substrate size (panel level package) from 300mm to 600mm to quintuple the area ratio and reduce FO-WLP production cost.
Ulvac’s new dry etching system for 600mm substrate features an improved plasma source, which enables fast and low-temperature etching of resin layers that was impossible with the existing capacitive coupling plasma (CCP) method.
The company’s plasma source can be applied to fluorine gases to enable the removal of seed layer titanium (Ti) etching, which requires a wet process, without side etching.
In addition, the NA-1500 machine can conduct silicon dioxide (SiO2) and silicon nitride (SiN) etching.
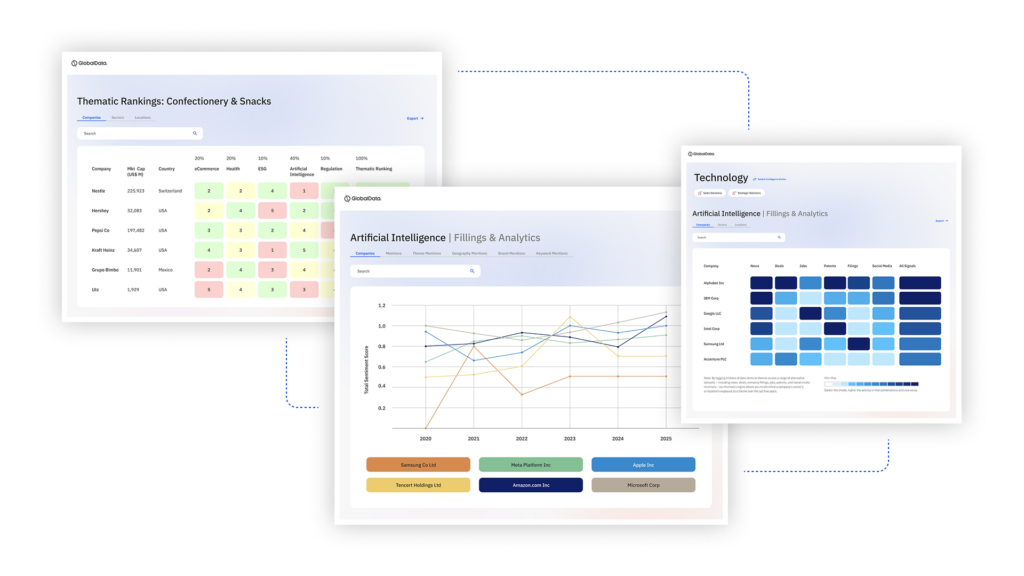
US Tariffs are shifting - will you react or anticipate?
Don’t let policy changes catch you off guard. Stay proactive with real-time data and expert analysis.
By GlobalDataThe new dry etching system can also provide stable transfer and processing without abnormal discharge.
According to Ulvac, its NA-1500 system can be used in Desmear applications, which remove residue (smear) in via formation with a laser drill.
Apart from resin material ashing, the system can be used in surface treatment (hydrophobicity from / to hydrophilicity) and pre-treatment for the wet processes, such as plating and others.
It can further be used for pre-treatment of underfill.