
20 years ago the barcode transformed the shopping experience with improved availability and pricing accuracy, while greater efficiency brought lower prices. Barcodes also made life easier for staff, freeing them up to spend more time with customers.
However, new developments are bringing greater visibility to the supply chain. Radio barcodes provide accurate and near real-time visibility of all products sold, right down to the individual item.
Tesco believes that monitoring this new level of visibility throughout its supply chain, from the factory to the store – often without human intervention – will lead to a world where stock counting and checking deliveries at the back door will become a thing of the past.
Tesco has been testing radio barcode technology for over two years thanks to its involvement with the EPCglobal centre, which has been responsible for driving standardisation and cost reduction. Following much internal analysis, research and trials, Tesco now understands how radio barcodes can be used to benefit its customers.
It has developed business cases and run trials to show that the technology actually works. It has also entered into partnerships with leading radio barcode technology companies to help it harness the radio barcode’s potential in real-life applications.
HOW DOES IT WORK?
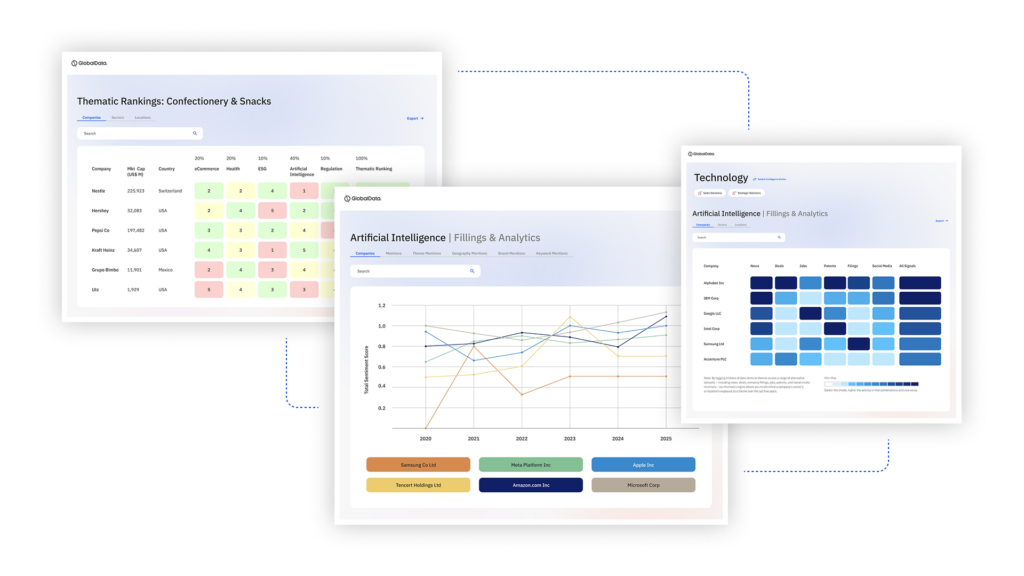
US Tariffs are shifting - will you react or anticipate?
Don’t let policy changes catch you off guard. Stay proactive with real-time data and expert analysis.
By GlobalDataProducts that Tesco wishes to track within its supply chain, including cases of products, pallets arriving from suppliers, reusable product trays and individual products, will have a radio barcode attached.
Radio barcode readers will then be placed at points across Tesco’s supply chain – at distribution centres, for instance, so it knows what products have been delivered, or on a shop shelf so it knows when to restock.
This will give Tesco visibility of all of the products within its supply chain, enabling it to transform the supply chain for the benefit of its customers.
At the supplier’s manufacturing or packaging plant, radio barcodes will be added to cases, pallets or individual items. This will be done either by attaching the radio barcode as a label or embedding it into the packaging material.
Each radio barcode is then given a unique number, which means it can be tracked around the supplier’s supply chain.
When an order is picked for delivery to a retailer, it can be checked and verified by radio barcode readers at loading bay doors. This means that the supplier knows he has correctly fulfilled the customer’s order.
At the retailer’s distribution centre, as the order is unloaded, it can be checked and verified by readers at its loading bay doors. This ensures that the retailer knows exactly what has been delivered.
This real-time information could be used to direct part of an order directly to a lorry being loaded for delivery to a store, for example. At the store, with radio barcode readers on the shelves, Tesco can monitor on-shelf availability to ensure that products are always on sale for the customer.
As customers remove products from the shelf, the system will be able to tell replenishment teams that this product needs to be restocked. If replacement stock is in store, they will be directed to where it is quickly and accurately. If there is no more stock in store, the system will know which products are urgently needed and will alert staff, enabling them to order more of these and replenish the shelves.
With full visibility of products within the supply chain, Tesco will be able to transport and stock the right products at the right time to ensure the shelves are always filled.
BUILDING A BETTER SUPPLY CHAIN
The technology has come a long way since Tesco first started working on secure supply chain. There has been continued development of radio barcode technology within retail and the project has moved onto the next phase of development – unit of delivery.
Secure supply chain proved that the technology works and that it can deliver clear benefits, offering greater visibility of the supply chain and a simpler process for staff and customers through improved availability, better service and cheaper prices.
Unit of delivery will build on what Tesco learned from secure supply chain. Unlike secure supply chain, which was limited to tagging trays delivering high-value goods such as razor blades and mobile phones, unit of delivery will see the tagging of returnable transport items delivered to stores from distribution centres.
Initially this will be cages and dollies, but in the future Tesco will include all returnable transport items. This will enable the group to cover a much larger part of its business than it could with secure supply chain.
Initially, unit of delivery will be implemented in one depot and 40 shops. Tesco intends to roll it out to all shops and depots in the UK in the next few years.
Tesco continues to work with standards bodies to find global solutions to the challenges presented by this new technology. The technology continues to evolve and the retail giant has made great strides forward in developing appropriate solutions to meet its business needs.