
Packaging machines today play a vital role in industries ranging from food and beverage to pharmaceuticals, electronics to cosmetics.
With ever-increasing demands for efficiency, precision and environmental responsibility, manufacturers are turning to automated packaging machinery to meet evolving market needs.
This overview explains how advanced packaging equipment influences production processes and sustainability goals, highlighting key trends and practical benefits.
Intelligent automation and efficiency gains
Driven by rapid production needs and tight margins, modern packaging machines come equipped with intelligent automation features that dramatically boost efficiency.
High-speed filling and sealing systems can handle hundreds of units per minute, while smart sensors detect anomalies—such as missing labels or underfilled bottles—reducing waste and avoiding costly recalls.
Integration with factory control platforms enables real-time monitoring of throughput, downtime and maintenance needs, allowing teams to optimise performance proactively.
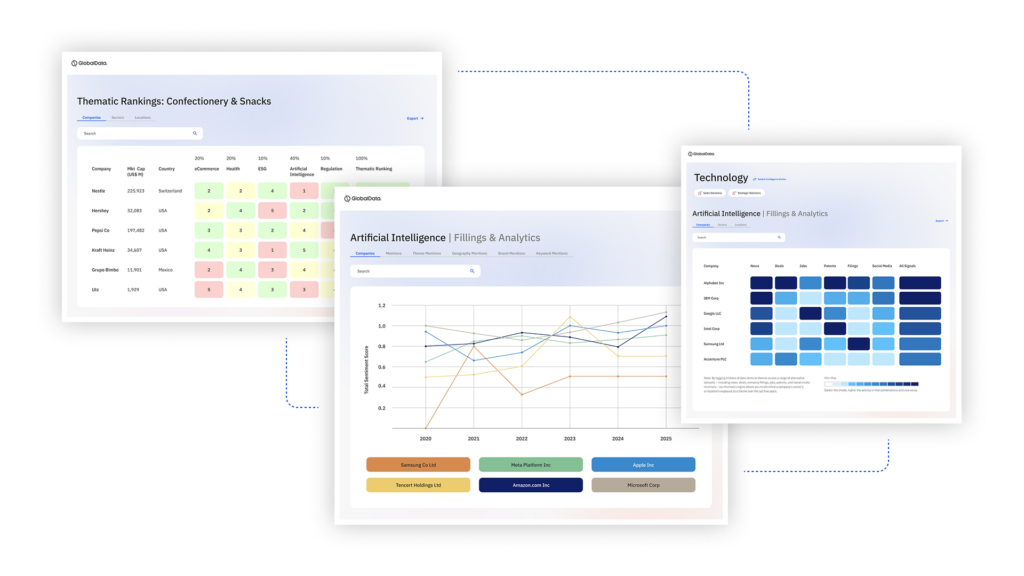
US Tariffs are shifting - will you react or anticipate?
Don’t let policy changes catch you off guard. Stay proactive with real-time data and expert analysis.
By GlobalDataMoreover, flexible packaging machinery adapts to different product types and formats with minimal downtime. Quick-change capabilities mean brands can produce pouches, cartons or tubes in a single line by swapping modular parts.
This versatility supports small batch runs and seasonal products without committing to multiple dedicated systems. The result is less idle time, fewer errors, and lower unit costs—essential in a competitive landscape.
Eco-conscious design and material reduction
As sustainability concerns drive consumer and regulatory pressure, packaging technology has pivoted toward eco-conscious design. Today’s packaging machines support lightweight packaging formats, such as reduced-thickness films and plant-based biodegradable materials.
With precise tension control and consistent heat sealing, modern equipment ensures packaging integrity even while using thinner substrates, helping brands cut material use and greenhouse-gas emissions.
Optimisation software integrated into packaging machinery analyses film roll consumption and goal alignment with waste-reduction targets.
Overwrap systems that once wrapped individual units in plastic are being replaced by cardboard-ready high-speed cartoners, which reduce plastics in favour of recycled paperboard.
More broadly, automation enables closed-loop systems where offcuts or scrap materials are captured and reprocessed, cutting waste and lowering disposal costs.
Smart connectivity and predictive maintenance
Another major advantage of current packaging equipment is smart connectivity. Packaging lines are increasingly linked via IoT protocols to centralised platforms, providing manufacturers with dashboards and alerts for predictive maintenance.
Rather than relying on calendar-based servicing, machines equipped with sensors monitor vibration, temperature and motor output to forecast potential failures. Engineers receive alerts to intervene before breakdowns occur, reducing downtime and lengthening equipment life.
Such connectivity also facilitates supply chain traceability. With batch-level data capture at each stage—filling, labelling, coding—products can be tracked from production to retail shelf.
Real-time serialization ensures compliance with regulatory standards in pharmaceutical and food industries, while recalls can be fast and accurate. Data insights on cycle times, throughput and efficiency enable ongoing process refinement and benchmarking.
Balancing cost and adaptability
Investing in packaging machinery requires a thoughtful balance between capital cost and long-term flexibility.
While fully automated, high-end systems deliver significant throughput and precision, smaller businesses might find that semi-automatic or tabletop packaging equipment offers a more affordable entry point.
These systems can be upgraded over time, supporting gradual expansion and limiting upfront expenditure.
Leasing and renting options are becoming more popular, allowing brands to try new technologies—such as robotic pick-and-place systems—without fully committing upfront. Leasing arrangements often include maintenance and training, giving manufacturers a more scalable approach.
Meanwhile, machine retrofitting services let companies upgrade legacy packaging lines with sensors, PLCs and control-system enhancements to capture the benefits of automation without full replacement costs.
Training and workforce evolution
The move toward advanced packaging equipment influences workforce skills. Operators now work alongside automated systems, handling quality control, troubleshooting and line changeovers rather than manual packaging tasks.
As a result, training programmes focus on digital literacy—PLC programming, HMI operation, basic robotics—while emphasising real-world skills like hygiene compliance, downtime response and safety procedures.
Manufacturers are partnering with technical colleges and engineering hubs to support apprenticeships in packaging automation. Upskilling existing staff ensures knowledge is retained in-house, while new recruits enter the workforce already familiar with IoT platforms and smart equipment.
This investment in talent development helps maintain both productivity and system safety across the packaging line.
The future of packaging technology
Looking ahead, packaging machinery is set to become even more adaptive and sustainable.
Emerging trends include AI-enabled vision systems that inspect products individually, blockchain-backed traceability for secure supply chains, and multi-lane systems that allow simultaneous filling of different SKUs on one platform.
3D printing integration could see packaging tailored to specific orders or regions, reducing warehouse stock and waste.
In parallel, demand for chemical-free, recyclable packaging formats will push machine-makers to innovate sealing and handling techniques. Machines capable of dosing water-based adhesives or heat-free closures will become more common.
Europe’s Green Deal and UK packaging waste regulations are adding pressure to reduce packaging weight and increase recyclability—and modern packaging equipment is the tool to make this happen efficiently.
Looking ahead
Packaging machines today are pivotal in enabling manufacturers to meet efficiency targets, navigate sustainability goals and maintain compliance in complex global markets.
Whether investing in fully automated lines or upgrading existing systems with smart features, companies can profit from faster production, reduced waste and better supply chain intelligence.
As machinery becomes more connected, flexible and environmentally conscious, its role in shaping future packaging strategies will only grow stronger.
High-performance packaging equipment isn’t just about sealing and filling—it’s a linchpin in delivering value, quality and responsibility to businesses and consumers alike.