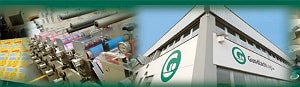
Inks are an indispensable necessity for every printing process. Moreover, for customers of label printing plants the exact reproduction of corporate colours and images is counted among the most widely discussed quality criteria. In particular, manufacturers of branded goods are extremely sensitive in this regard. Its no wonder then that Frank Neumann, managing director of Logo Etiketten GmbH in Mahlberg in the Southern Baden region of Germany, describes printing inks and the corresponding operational environment as the heart of a label printing plant which should not be substantially modified without good reasoning.
The implementation of low-migration label production for the food market segment was just such a reason for Logo Etiketten. This article reports on the background and the practical experience with the production-wide introduction of low-migration inks and varnishes and the concurrent conversion to the mono-pigmented ink system of printing ink manufacturer Zeller+Gmelin.
The printing plant Logo Etiketten, specialised in adhesive labels and packaging, is part of the Gundlach-group, an association of specialised companies in the printing and publishing industry with more than 850 employees. At the two locations Mahlberg/Baden and Weinstadt/Stuttgart, Germany, Logo Etiketten generates an average annual turnover of EUR 13 million with around 85 employees.
The scope of supply ranges from digital prepress via flexographic and screen printing on presses with a maximum of ten inking units and includes finishing options such as hot and cold stamping, varnishing, coating and lamination through to further processing, such as cutting and finishing.
A relatively high proportion of the clientele comes from the food and beverage sector. Thus, the company regularly has to deal with declarations of conformity customary within this industry. They continuously receive demands from customers to sign generalised guarantees for the supplied labels. Even though Logo Etiketten rejected each of these requests, the company felt already years ago obliged to investigate this topic more intensely. Since European legislation is increasingly focused on the role of packaging with regard to the question of food safety, Frank Neumann is convinced that this will sooner or later lead to a binding rule to prescribe the use of low-migration ink systems. To guarantee acceptable product safety with conventional inks, material and processes will by far exceed the technical capabilities regarding measurement procedures and control methods, as well as the chemical know-how of most label and packaging printing plants.
Future-proof solution wanted
Against this background, in 2008, Logo Etiketten began to search in the market for a solution for UV-flexo printing outside of traditional ink systems. A suitable partner was found with the printing ink manufacturer Zeller+Gmelin from Eislingen, Germany, from which the company already purchased water-based printing inks for special applications. In January 2010, the decision was made for an ambitious project with an investment in the high six-digit Euro range. "The amount covers a very extensive complete package", explains Frank Neumann.
"In the end, with this project we pursued several objectives at the same time. We wanted to convert the entire production to a low-migration operation and simultaneously implement the most resource-saving use of the printing inks and at the same time increase automation and standardisation of the ink mixing process." Finally, this implied the construction of suitable premises, the fitting of a new ink kitchen, including the installation of an ink mixing unit with 14 stations from Fluid Solutions, the implementation of the ink management solution Ink Formulation from X-Rite, a print-proofing system with UV-dryer and more.
Frank Neumann can put forward good reasons for the radical step to change over the entire production at the same time. Mixing production on one press, that means changing between standard printing inks and low-migration inks, is not a realistic solution from his point of view. As numerous field tests have proven, even with extremely thorough and very time-consuming cleaning, contamination of the low-migration production is difficult to avoid. Moreover, in the end it does not pay off due to the extensive cleaning effort required.
The use of a single printing press as an exclusive production line for low-migration orders was out of the question for Logo Etiketten, due to the technical set-up of the presses. The web widths and configurations of the individual press lines are coordinated with the order structure in such a way that a concentration of the jobs with low-migration inks on one or two presses was not realistic. The logical consequence was the decision in favour of a complete conversion.
Two objectives achieved with one conversion
One project which had already been considered at Logo Etiketten was the changeover from PMS (Pantone Matching System) to a future-oriented concept like the mono-pigmented ink system of Zeller+Gmelin. Since a complete reformulation of all colour shades by means of a spectrophotometer and PC was required due to the conversion to low-migration inks anyway, at least this part of the system change could be completed in one go.
"Nevertheless, we had a healthy respect for this decision. After all, we wanted to turn inside-out the heart of our printing plant at two positions at the same time", admits Frank Neumann. "We were well aware that with such a complex project it is not possible to remove all obstacles beforehand. But we were reluctant to shoulder the effort for the adaption of the approximately 4,000 to 5,000 formulations twice."
In retrospect, the transition period of about six months which started in May 2010 with the start-up of the new ink mixing unit went virtually according to plan even though from time to time unforeseeable obstacles had to be overcome, remembers the Production Manager, Michael Jagiella. "Here, the close collaboration with Zeller+Gmelin played a decisive role. The support in terms of employee training and preparation of formulations was very effective and competent."
However, for the printing ink manufacturer this project also proved to be a challenging job. While in the beginning the development of the low-migration inks concentrated on their application in the food sector, the low-migration ink system now had to be made ready in a short period of time to meet the requirements of all areas of application in order to enable Logo Etiketten to realise the complete conversion.
Only with specialities, for example special effect inks, special varnishes, laminating adhesives etc. was there a need for further development. In the opinion of Ulrich Höfler, who as Area Sales Manager for Southern Germany was in charge of the introduction of the new ink system at Logo Etiketten, the work was worth the effort: "As a result, the low-migration ink system is highly developed with regard to properties like reactivity and ink adhesion so that now label printing plants can use it for their entire production."
Minimisation of mixing errors and ink residues
With the selection and introduction of the automatic ink mixing facility the label specialist from Mahlberg proceeded as with the entire subject matter of printing ink. An objective here was to increase productivity by further automation and standardisation of the ink mixing process.
The supply of printing inks with the respectively correct colour shade and in the required quantity is of vital importance for smooth production. If mistakes are made at this stage, this can result in expensive machine stoppages. For this reason, Logo Etiketten has put the responsibility for this work area on two experienced printers, with very reliable colour evaluation experience, who work in a two-shift operation.
To ensure problem-free processing of the low-migration and mono-pigmented inks in the plant, the technical equipment was coordinated with the ink supplier. Marcus Ruckstädter, sales manager at Zeller+Gmelin, points out that an important feature for instance was the compatibility with SQL-based databases, so that the dosing system could for example be directly controlled via the Ink-Formulation software from X-Rite. Furthermore, the system is integrated into the production data acquisition and area coverage management. In this way, the required quantity of individual colour shades can be calculated by the system in case of follow-up orders.
In addition, the ink manufacturer suggested equipping the plant with an agitator in each container or – like with the mixing system of Fluid Solutions – with a recirculation system. This was to ensure that even when mixing inks with a somewhat more viscous consistency, one could reliably produce consistent mixing results.
With their target for the most resource-efficient production, Logo Etiketten is also able to tackle a reduction in the volume of ink residues with the use of the ink mixing facility. In the first year, the printing plant already succeeded in considerably reducing the production of ink residues. This means that a significant share in the reduction of waste costs of about 25% is attributable to the ink mixing facility.
Improved sustainability
From what he knows today, Frank Neumann would again make the strategic decision to carry out a simultaneous double conversion with such far-reaching consequences in the area of printing ink and ink supply which is such an essential one for printing plants. Experience to date shows that having taken these steps a strengthening of the company’s sustainability could be accomplished as planned. In the future, label printing plants will hardly be able to avoid the changeover to low-migration ink systems. Current developments obviously indicate that EU-legislation will demand this to happen sooner or later.
Migration – a multifaceted subject matter
In the label and packaging industry the keyword "migration" is a subject matter that repeatedly comes up at trade fairs and congresses as well as in the media. But as prevalent as the discussion on low-migration label production may be, as great is also the uncertainty of many printing plants. Many a company management is not aware of the risks and expense that can result from a careless signature on a guarantee declaration, if the label production does not comply with the complex food law requirements in practice.
In contrast, the printing plants which have already adapted themselves in an exemplary manner to the situation, for instance by converting to low-migration ink systems, are facing other economic challenges. A look beyond the borders, says Marcus Ruckstädter, sales manager at Zeller+Gmelin, reveals a very different handling of relevant regulations. Companies like Logo Etiketten are confronted with that fact every time label printing plants from other countries with a more lax attitude regarding legal requirements are involved in offer comparison.
In all probability, these suppliers have more leeway in their pricing because the effort which would be inevitable for meeting the regulations are not being considered in their calculations. Especially with transnational transactions, this means an obvious distortion of the competition. Tolerably fair conditions can only be expected when end customers or authorities demand to see evidence that a signed declaration is in fact concretely covered, ensuring the compliance with regulations. The use of a low-migration ink system would among other things be part of such a package of measures.
A major obstacle to the widespread introduction of low-migration inks is to be seen in the considerably higher costs compared with standard UV-inks. Label printing plants and ink manufacturers are not able to pass on the total extra costs in the supply chain due to the fact that while end customers are certainly interested in having their labels printed with low-migration inks they do not accept higher prices.
There are several reasons for the higher expense of low migration ink production. For instance, the selection of raw materials is limited. In addition, the raw materials suitable for low-migration inks are generally considerably more expensive. At the same time, the effort for research and development is higher than average. For instance, Zeller+Gmelin recently used about a third of their r+d-capacity for the development and optimisation of low-migration ink systems.
Also in the production of these printing inks, considerable extra expenses arise due to the necessary provision of additional production capacities and increased set-up costs. This is why Zeller+Gmelin is currently investing in the expansion of production facilities which are specifically designated for the manufacture of low-migration printing inks and varnishes.
Many investments pay off in the long term through economic benefits. In the current situation, both the manufacture of low-migration ink systems and their use in label production equally do not hold water as a common argument.
Printing ink manufacturers and printing plants, therefore, are facing the same strategic decision: Conversion to low-migration systems – yes or no? Since according to the opinion of Logo Etiketten and Zeller+Gmelin there will be no alternative to low-migration inks in the future, both companies have set the course for a low-migration future.