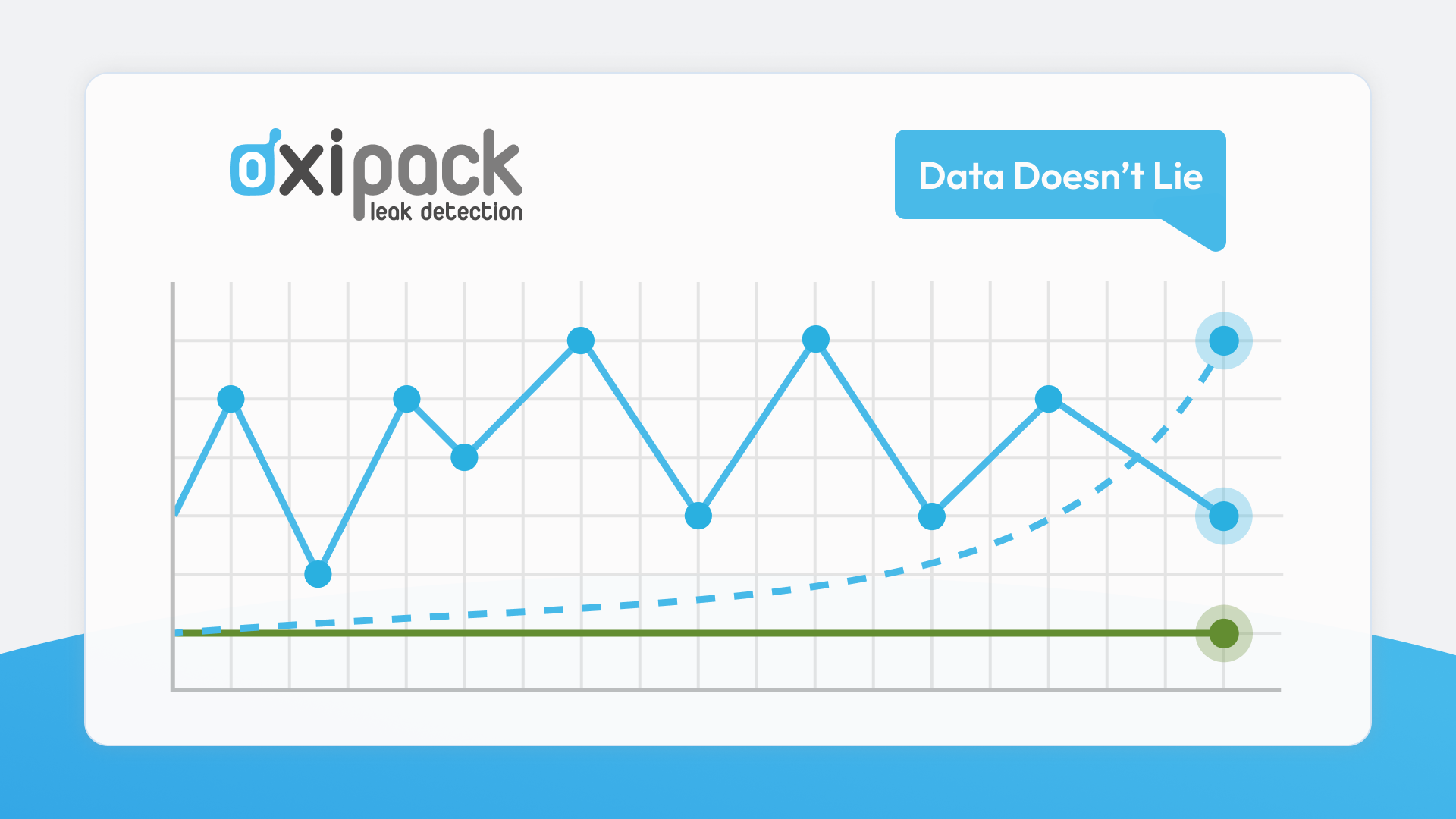
In our line of work, you often hear people say, “As long as it doesn’t leak, we’re good.” But what if we could go beyond good? What if we could use each leak test to learn, adapt, and improve the entire production process?
At Oxipack, we’ve built our vacuum decay systems not just to detect defects, but to generate real-time intelligence. Every test we run produces meaningful data. And that data is quietly transforming how manufacturers approach quality, compliance, and efficiency.
Data at the core of every test
Our systems measure pressure changes with millibar-level precision. Every cycle records:
- Start pressure and test duration
- DeltaP (pressure difference)
- Pass/fail outcome
- Timestamp
- Line, shift, or operator (if configured)
This might sound technical, but here’s why it matters: instead of relying on visual inspection or subjective judgment, you get hard data. You can trace exactly what happened, when, and where. The most critical value is the pressure difference between the starting pressure and the pressure at the last measurement point. That’s what tells you if a package is leaking, as well as the size of the leak.
As our data scientist Gerben Mooiweer explains: “The measurement principle of the Oxipack leak tester is based on pressure readings monitored over a set period. If the pressure increases too much, it’s caused by air escaping from the packaging, indicating a leak.”
Gerben adds, “We also log the test protocol, what we call the ‘recipe’, along with reference data like line or operator. All of this gives manufacturers full traceability.”
From monitoring to meaning
The insights don’t stop there. With our logfile analyser, you can track performance over time, spotting slow drifts or sudden spikes before they become real problems. We’ve even built an integration tool that continuously reads and visualises data from each leak tester in real time. When something goes off, the operator sees it instantly.
This setup is already helping one of our major snack industry clients detect production anomalies early, adjust processes, and avoid recalls. It’s not just smart. It’s operationally transformative.
Better than bubbles
Compared to traditional methods, like bubble or dye testing, our vacuum decay method is deterministic. It doesn’t rely on interpretation or hope. There’s no guessing, no inconsistent results, no missed microleaks. Everything is tracked, stored, and ready for analysis.
“We measure multiple points to determine early results and even stop the test if the leak is too large,” says Gerben. “Deviations in pressure trends also prove the linearity and repeatability of our system.”
Visual tools that make a difference
We have also developed a suite of analysis tools to bring our data to life:
- The Leak Detection Test Simulator is a statistical tool designed by Oxipack to help predict and analyse the outcomes of leak detection tests over a specified period and number of products. This is particularly useful for quality control professionals who need to estimate the likelihood of detecting leaks based on the expected leak rate and the number of products tested.
- The Leak Flow Rate Calculator, developed by Oxipack, accurately determines leak flow rates by analysing pressure changes over time, measured in millibars (mbar). It is especially valuable in sectors such as food packaging, where precise leak detection is essential to reduce product loss and maintain quality standards.
- Logfile analyser a powerful application designed to help analyse and visualise data from leak detection processed. The Oxipack Logfiles Analysis Tool features several tabs, each tailored to different aspects of logfile analysis, making it easier to monitor and optimise your leak detection efforts.
Gerben highlights the impact.
“The Measurement Plot visualises how DeltaP changes over time and shows exactly where a package falls in relation to the leak/no-leak threshold. It gives a clear picture of performance trends.”
These tools run on internal or customer-hosted servers and can also be integrated into a company’s own network through our Data Integrity Tool (DIT).
The bigger picture
For us, this isn’t just about catching leaks – it is about giving manufacturers the tools to truly understand their packaging process. The data helps validate new designs, support preventive maintenance, and deliver transparent quality reports that stand up to any audit.
Gerben sums it up: “You don’t want to discover packaging failures months later. With our system, you see them in real-time and act immediately.”
We’re not here to scare anyone into changing systems. We’re here to show what’s possible when your leak tester becomes a window into your line’s performance.
Because when you have the right data, you’re not just checking for defects. You’re building smarter processes. And that’s what modern manufacturing needs.