Disagreement on major issues might seem inevitable when you bring together five senior people from different companies in flexible packaging. However, there is a remarkable degree of agreement for an industry sector that is still very diverse.
While Australia’s Amcor has led the acquisition process to create larger packaging operations, many others have followed suit. The flexibles industry is consolidating, but there are still many niche players. Everyone at the Round Table agrees the consolidation process will continue, but niche players will remain and can prosper.
There is agreement, too, that growth rates in flexible packaging are set to continue (although at variable rates for different types of product), and that demand arises out of social change as well as technical capability.
There was also consensus on the environmental front, with the European Parliament debating some even stricter regulations, to be introduced by 2008, under which companies will have to show that their packaging is, ‘the environmentally best option’. Positive attitudes to improved environmental performance outside the plant and to health and safety practice inside are common to all five panellists.
Changing world fuels demand
The appeal of flexible packaging to the consumer is one of the drivers that everyone in this rapidly growing industry has analysed and studied. Social change seems to be the key factor driving demand, including the growth of the single-occupant home, as well as the demands of time management in an affluent society.
Ole Ostergaard, the owner-manager of specialist laminator Ehrno, in Denmark, is sure that demand for flexible packaging, especially for food, will continue to rise, and that activity levels are being directly affected by changes in the consumer market. ‘The speed of change is increasing and we find ourselves making quicker responses in the business. People don’t cook like they used to, and the increased number of single-person households is creating a new lifestyle. We are a small company in an industry where company sizes are going up fast and that can seem like a challenge, so we try to do even more R&D than our size warrants.’
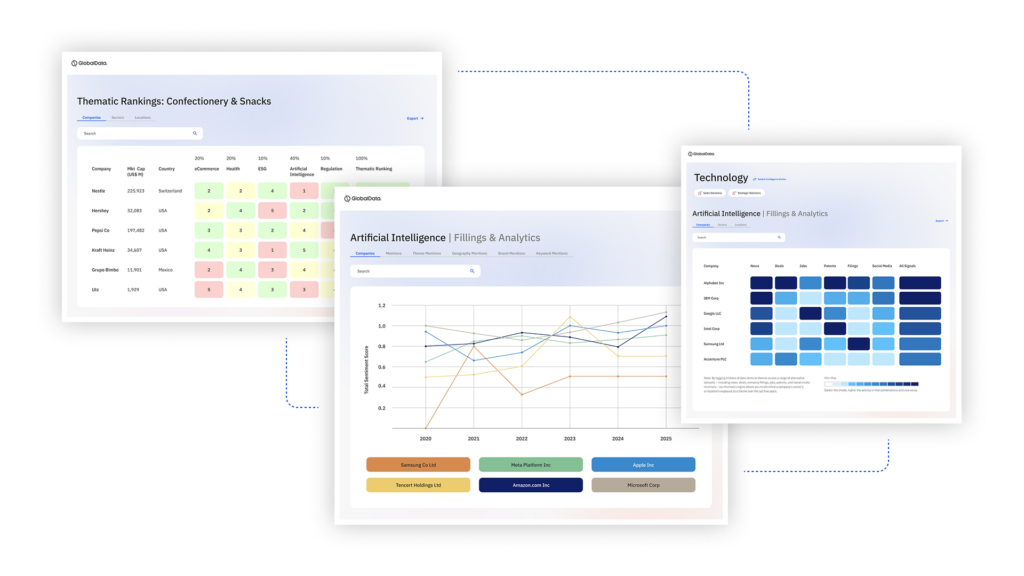
US Tariffs are shifting - will you react or anticipate?
Don’t let policy changes catch you off guard. Stay proactive with real-time data and expert analysis.
By GlobalDataRaw materials supply difficulties
Companies seeking growth in printing and converting want to be in the consumer packaging market, and the converters are feeling the effects on their supply side. Raw materials, with availability already adversely affected by production problems at petrochemical plants, are in high demand, especially from China. Resin has seen dramatic price increases. Polyethylene resins are double the price they were a year ago and films are 50 per cent up, say our participants.
Parts of the flexibles market are growing at different rates. There is annual 10 to 12 per cent growth in pouches, yet demand for frozen food packaging is growing at only 2 to 3 per cent. Clearly some markets are more mature than others, but they are all feeling the effects of the current position of raw material prices.
Andrew Riley is managing director of Mondi Packaging Wheatley Ltd, the UK flexibles division of the group that is mainly involved in providing packaging for human food and pet food manufacturers. He is speaking for everyone in packaging when he says, ‘The pressure on margins is as strong as it has ever been. The brand owners and retailers who take the product don’t want to pay more and the petrochemical companies dictate raw material prices. Our suppliers indicate continued pressure on prices in the first quarter of 2005, with possibly more stability in the second quarter. We are certainly not likely to see prices fall, although demand may ease towards the end of the year.’
Greg Coughlin is the market development manager in the appearances and performance technologies group at Engelhard Corporation, the specialist US laminated film manufacturer. He says, ‘Increased resin prices have put the squeeze on everybody and as a result added value is required to offset the costs. To add on material costs is problematic otherwise. Resin prices rose recently to a new all-time high and linear low-density polyethylene has especially risen in price. That particularly affects the multi-layer film manufacturers. Demand from China for raw materials to feed that nation’s economic growth is a major factor, and until oil prices are stable, the trend seems likely to continue.’
Companies at the commodity end of the market are feeling the squeeze in the current climate. Cost pressures in the UK no doubt played a part in the demise, mentioned by several participants, of a UK company that manufactured bread bags and toilet tissue overwrap. Smaller companies in Europe are feeling the pressure and some will succumb, thus reducing capacity in the coming year while resin prices stay high.
Researching improvements
The marketing strategies of the major supermarket groups and brand owners supply one set of stimuli to the manufacturers, which continues upstream to the technology and the R&D that enable improved performance in packaging applications and materials. All our participants stress the importance of R&D to the continued success of their companies.
Guido Bisch, business team head packaging at Treofan, says, ‘We have close relationships in development work with our end users, including Nestlé, Danone and Masterfood. The key issue for our customers is simplicity, and that is why multi-layer technology is increasing in importance. If we can produce a multi-layer film that avoids the need for secondary processes such as coating, metallising or laminating, that will save the end user time and money. We are currently producing seven-layer film at our pilot plant, putting us at the forefront of the technology.’
The high price of materials has sharpened the competitive nature of the marketplace. The result is that companies are increasing investment in R&D to find the added value that will provide them with competitive leverage. Customers will only pay more for improved products with better functionality. The emphasis is thus on developing ‘intelligent’ packaging solutions, including films for controlled atmosphere, breathable and heatable applications
Company consolidation
Several members of this round table have suggested that the dynamic of the flexible packaging business is changing rapidly and dramatically on the twin pillars of growth and consolidation. Two of the six companies that agreed to take part in this discussion have changed their names since, a reflection of the pace of mergers and acquisitions in packaging as growth-minded companies seek a larger market share.
Mondi Packaging formed only four years ago is already the seventh biggest flexible packaging company in Europe, with turnover up from €200m to €2.8bn. The company plans to be in the top five by the end of the decade. Treofan, a global supplier of polypropylene film, is an amalgamation of three companies in film manufacture with operations in Europe, the USA, Mexico, South Africa and Australia. ANInks is merging with BSF to create a larger presence in the international inks market.
Organic growth, even in an expanding sector, is harder to achieve than growth by take-over and amalgamation.
In the pipeline
The longer the international boom in demand for flexible packaging continues, the more likely it is that on the printing front, flexographic, traditionally seen as inferior in quality to offset, will continue to gain ground. On a flexo production line, converting follows print, while folding cartons on offset still have to be set aside for 12 to 24 hours’ drying time. So flexo has better in-line capabilities. In general it is also easier and less costly and, despite its drawbacks, it will continue to grow.
Guido Bisch of Treofan says his company introduces new and improved products every year and is currently working on a new film with nanotechnology to produce a micropore product. Greg Coughlin of Engelhard Corp predicts that heat-sealed pouches will replace other fastenings, and that barrier performance, flexible multi-layer film and high-heat properties will be the key technologies in the coming period.
The most important performance parameter for the end user in selecting a packaging solution is faster throughput at lower costs. The question is just how far can performance improvements be taken. On the other hand it is getting increasingly competitive on the store shelves, so eye-catching looks to increase brand share will be another major factor. Counterfeiting is very much on people’s minds at the higher end too. Unique or unusual materials make packaging harder to copy. Just a few obstacles at the right level can deter counterfeiters because they move on to something easier to pirate.
Environmentally sustainable
The social emphasis on sustainability is clearly felt by all our participants and they take their responsibilities seriously. Alongside environmental practice, Health and Safety practice is increasingly the subject of close attention. Andrew Riley of Mondi Packaging tells us, ‘We absolutely see sustainable practice as a competitive advantage. Sustainability is a corporate must for the whole Anglo-American group. All our plants control emissions and there is a very strong ethic on sustainability. We can extrude biodegradable resins and we are working on down-gauging both paper and plastics to reduce materials usage and thus cost, at the same time as reducing the environmental impact.
‘We are investing capital heavily in the latest equipment, which tends to be more environmentally friendly, more energy efficient and more productive. The bottom line continues to be critical, but the first item on any board meeting in the group is health and safety.’
Ole Ostergaard confirms that Ehrno is working on thinner materials and easier disposal. ‘Clearly flexible packages are easier to dispose of than cans. We operate in Denmark and the UK and there is a lot of difference between the two markets. I believe that, in recycling, Denmark is well ahead of the rest of Europe. A lot of waste is incinerated and environmentally that has reduced landfill. The materials involved in flexible packaging produce less volume and weight for disposal than cartons, metal or glass, and that advantage is good for us as a company and good for the environment.’
‘Our answer to sustainability, recycling and environment is Biophan,’ says Bisch of Treofan. ‘This film is made of polylactic acid (PLA) and therefore biologically degradable. Biophan, made of the renewable primary product starch, is completely degradable into carbon and water.’
Such products combine aesthetics and environmental conscience. This will appeal greatly to consumers.
A softening of margins
The picture that emerges from the PCI Round Table shows that companies from the smallest to the largest are positive and optimistic about the future, despite the current problem of pressure on margins.
Antonio Grassotti, the CEO of Mondi Packaging, sees light at the end of that tunnel. He suggests that although prices are unlikely to fall soon, and smaller companies especially in Italy are going under as a result, increased capacity is on the way.
New capacity for resins in Oman, Russia and China will come on stream and the tight situation on raw materials will ease, perhaps by the end of 2005, but definitely in 2006.
Participants
Ole Ostergaard is the owner manager of Ehrno – one of only two laminating companies that remain locally owned in Denmark. Eighty per cent of the business is in packaging for foodstuffs (the remainder in technical laminates) for markets in Denmark, the UK, Germany, Scandinavia and some Benelux countries.
Greg Coughlin is the market development manager, in the appearances and performance technologies group, at Engelhard Corporation, the specialist US laminated film manufacturer with a growing presence in labelling, tamper-proofing and surface decoration.
Andrew Riley is the managing director of Mondi Packaging Wheatley Ltd, the UK flexibles division of the Mondi Packaging Group, which has its European HQ in Vienna and plants in the UK, Denmark, Germany, Poland, Hungary, the Czech Republic and Italy. Mondi is part of the giant Anglo-American Group. Mondi Packaging CEO Antonio Grassotti also contributed.
Guido Bisch is business team head, packaging at Treofan, the international film manufacturer that is a consolidation of three firms with operations in Europe, the USA, Mexico, South Africa and Australia. In terms of volume of production Treofan’s only competitor is ExxonMobil.