Much has been said about the differences between cold, hot, sterile, aseptic and extended-shelf-life filling of dairy and fruit beverages and related fluid food products.
The machines used in this sector are enormous electromechanical engineering marvels that marry products with plastic bottles and, increasingly, manufacture the plastic bottles before or during the packaging process.
Today, most high-output beverage packagers have installed capacity for polyester bottle manufacture from either purchased preforms or directly from resin into their own injection moulding machines.
Suppliers such as Husky for injection moulding machines and Sidel for stretch blow moulding equipment have led a successful transition for the large-unit volume users and are now targeting the smaller companies.
In 2004, two plastics are dominant for plastic bottle making for fluid foods: high-density polyethylene and polyester. For economic and efficiency reasons, in- or off-line bottle making is fairly common.
Now, new systems are appearing in which the bottle making is even further integrated: upstream with resin, and downstream with bottling. Both systems are increasingly connected with aseptic and ultra-clean operations – for sterile or extended-refrigerated-shelf-life beverage contents.
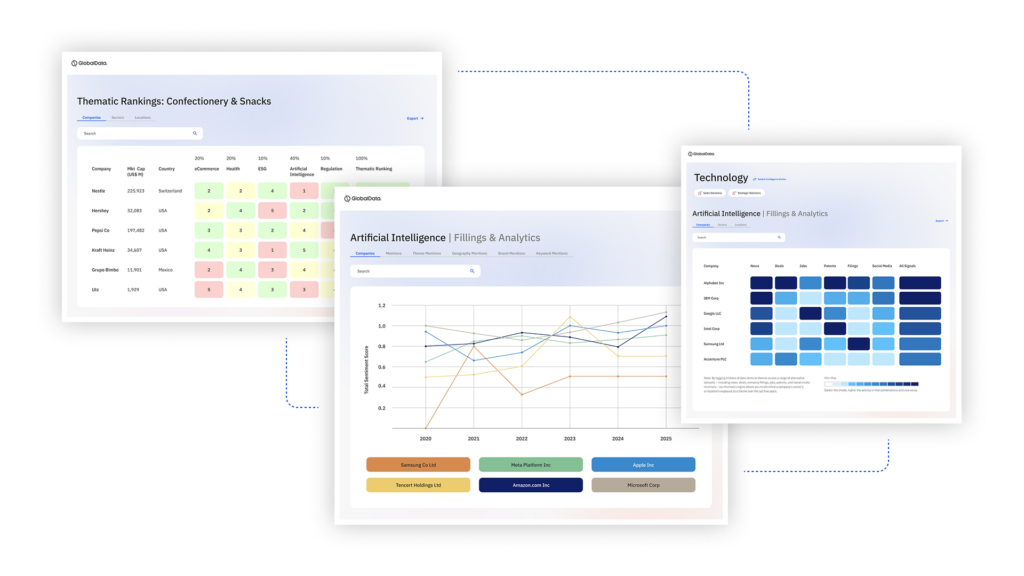
US Tariffs are shifting - will you react or anticipate?
Don’t let policy changes catch you off guard. Stay proactive with real-time data and expert analysis.
By GlobalDataFrom resin to filled bottle
What are perhaps the most advanced systems begin with thermoplastic resin pellets that are melted, at usually microbicidal temperatures, to produce an extrudate forced through circular or near circular dies.
The oldest and evidently most reliable system comes from Germany’s Rommelag, which produces Bottlepack® blow mould fill-and-seal equipment in which the heat of the plastic melt sterilises the bottle interior. This equipment is used for monolayer extrusion blow moulding of high-density polyethylene (HDPE) bottles.
The resulting bottles are one-time opening, because the closure is unitary with the bottle body. Such systems limit the packager’s flexibility and output: mould sizes and shapes are essentially fixed.
Polyester resin is now being fabricated into test-tube-shaped preforms for downstream blowing and filling on a single closed line. Italy’s SIPA has engineered such a system, which involves transfer under positive pressure of sterile air of the preforms within the enclosed area from injection moulder exit to stretch blow moulding and subsequently to the Italian Procomac (or other) aseptic bottle filling machine. The system, capable of an output of up to 600 bottles per minute, is largely employed in Italy for ambient-temperature, shelf-stable, high-acid beverages.
The Netherlands’ Stork system represents a variation on the resin-to-filled-bottle concept. Beginning with HDPE resin, the system extrudes and blows a closed monolayer bottle whose interior is sterile by virtue of the extrusion temperature.
In a sterile environment, the closed orifice is sliced off leaving an open-top bottle. The bottle is then flooded with hot hydrogen peroxide to sterilise both the interior and exterior. Under aseptic conditions, the bottle is transferred for aseptic filling that is distributed under conditions providing extended refrigerated shelf life.
Switzerland’s Elopak, in conjunction with extrusion blow moulding equipment maker Techne, now offers a range of HDPE bottle systems for beverages with extended refrigerated shelf life. Resin is extruded and blown into closed-mouth, sterile-interior bottles that are transferred under sterile conditions (for the interiors only) to the Elopak aseptic filling machines. In this equipment, the flashing seals are sliced off, exposing the sterile interiors for filling and sealing with pre-sterilised closures.
From preforms to filled bottles
Tetra Pak’s French Sidel and their filling machine company, Remy, have combined for an analogous integrated system. Sidel equipment forms the polyester bottles from preforms that are sterilised with hot hydrogen peroxide prior to blowing with sterile air. The preforms are transferred under aseptic conditions to the Remy filler. No bottle sterilisation is required between bottle blowing and filling, as the filler has been pre-sterilised and maintained sterile in a Class 100 cleanroom.
These systems are commercially employed to produce beverages of extended refrigerated shelf life and low acid content (often described as ultra-clean), but it is also applicable for sterile, ambient-temperature, shelf-stable high-acid beverages (aseptic) and high-acid beverages with extended refrigerated shelf life (clean operation). Bottle output ranges from 100 to 600 bottles per minute. Advantages of the preform-to-filled-bottle systems are total control, less total equipment and no bottle storage.
This article has been adapted from an article in Food Technology with permission of the Institute of Food Technologists.