The business of packaging medical devices is constantly changing. Not only are the materials used to pack devices becoming stronger, thinner, more protective and more flexible almost by the year, but the medical device regulators around the world are close, finally, to agreeing on international standards for the packaging of medical devices.
These standards will not only cover the actual packaging and labelling, they will also set out standards for testing the efficacy of the packaging and the methods used to produce it. What the industry wants is to have a regulatory system based on meeting performance standards rather than satisfying the regulators’ random testing of samples or lots.
The packaging of sterile medical devices is an unusual branch of the packaging industry. Medical device packagers are subject to tight regulatory standards that are aimed at ensuring the highest possible standard of care for the patient.
Unlike most forms of packaging, the package in which the medical device is transported and distributed serves little marketing function. Its main functions are as a communications tool and to protect the sterile package. On the other hand, the packaging around medical devices has to be perfect.
‘We cannot afford any failures,’ says John Spitzley. Spitzley is currently Medtronic’s fellow, packaging, and along with Curt Larsen, from DuPont Medical Packaging and Spartan Design Group, he has been heavily involved in the drive to set and raise the quality of international standards for medical equipment packaging.
In 2002, Larsen and Spitzley set up the Institute of Packaging Professional’s (IoPP) Medical Device Packaging Technical Committee, which they now co-chair. The committee has set up several task forces to deal with issues in medical packaging.
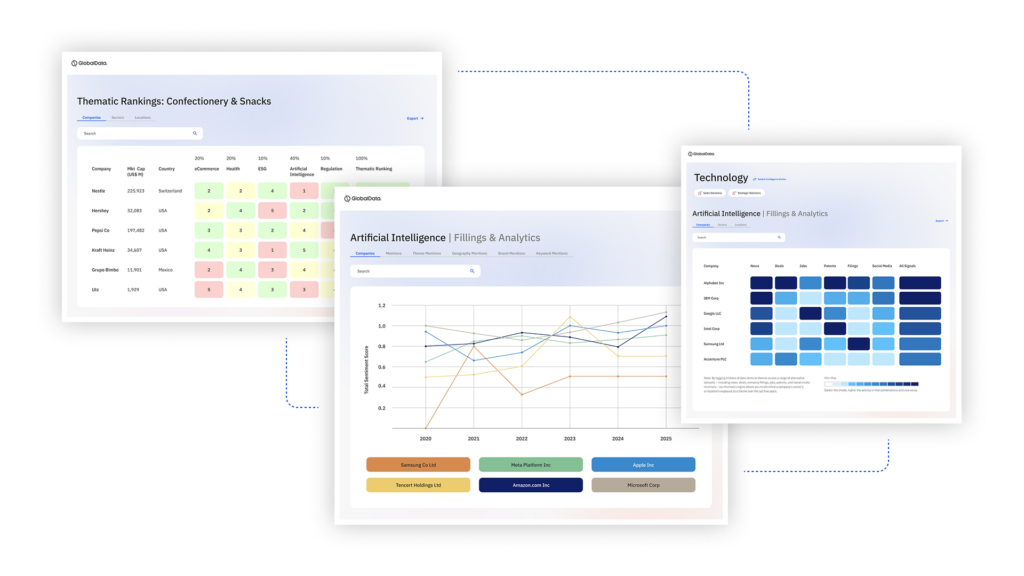
US Tariffs are shifting - will you react or anticipate?
Don’t let policy changes catch you off guard. Stay proactive with real-time data and expert analysis.
By GlobalDataThose failures in packaging that do occur are, in Spitzley and Larsen’s experience, usually the result of human error. ‘The recalls are mostly down to human error, generally to do with the labelling,’ Larsen says. ‘I can’t recall the last time there was a recall because of a problem with the actual packaging materials. The materials used in the medical device industry are extremely robust, and research shows that the failure rate is less than one in one million packages.’
The big difference, however, between medical device packaging and other branches of the packaging industry is the role the regulators play. Over the past 30 years, the industry has been shaped by the FDA. The FDA takes an interest in all aspects of medical device packaging from material selection, design and manufacturing to labelling and sterilisation.
Labelling for medical devices is crucial. The labelling has not only to identify what is in the package but also clearly set out instructions for its storage and use. Yet medical devices range from disposable items such as surgical gloves and catheters to life-saving devices such as pacemakers.
‘Often there are unique device requirements,’ says Larsen. Sterilisation is also an important issue in medical device packaging. ‘There are more and more devices where sterilisation is an issue,’ Larsen says. ‘We’re now getting pre-filled syringes, for example, and drug coated stents.’
Not only are more devices being sterilised, but the ways in which they are being sterilised are changing, and this has implications for the packaging that protects the device and preserves its sterility.
Over the past ten years, gamma and electron beam sterilisation have become increasingly popular. The increase in the use of radiation means that more packages are impermeable or non-porous. Another trend has been in using thermoformed plastic packaging, especially for orthopaedic devices.
Tight regulation
One key issue for the packaging industry is satisfying the FDA that its testing procedures for packaging are effective and robust. The FDA wants evidence that the packaging does what it is designed to do. The American Society for Testing and Materials International (ASTM) has designed testing guidance for the medical packaging industry. It has also published materials and package system test standards for medical device packages. Testing is one area of the medical device packaging industry in which global standards are being agreed upon.
The FDA’s Center for Devices and Radiological Health recognised this standard, ISO 11607, in 1998 as a consensus standard. This meant that the industry now knew what would satisfy the FDA, but they only had to demonstrate that they met the standard, rather than provide the FDA with test data for the packaging of different devices.
Environmental controls
The materials used in device packaging have changed considerably over the past ten years. Spitzley says, ‘lot of our materials are recyclable, and we’re very careful what we use. The core products are polyethylene, polyester and paper.’ He acknowledges that there are differences between the USA and Europe over the proportion of packaging that should be recyclable. ‘There are pretty aggressive recycling requirements for packaging in Europe,’ he says.
There are also growing requirements, especially in Europe, for packaging to be environmentally friendly. This has meant that some packagers have moved away from bleached to natural board for their cartons. Now, scientific improvements have made the bleaching process more environmentally friendly, so there has been a switch back to bleached board, which has produced an improvement in print quality on the package.
Another indication of the industry’s sensitivity to environmental concerns is that packages are invariably labelled with water-based inks. These are more environmentally friendly than solvent-based inks. Whenever possible, firms are looking to produce environmentally friendly packaging designs.
Careful progress
Although new materials such as films, high-performance papers, non-adhesive package systems and high-barrier products have all come onto the market and been adopted by device manufacturers, once manufacturers have found a packaging solution that does the job, they tend to stick with it. This is partly because the cost of altering the package is usually disproportionate to the benefit.
This does not mean that packaging is a backwater. ‘Packaging is not a minor issue,’ stresses Larsen. ‘A packaging engineer has to understand the stresses that the package will undergo in the distribution process and also the dangers ordinary things, such as light or moisture, pose to the device inside. If you get someone who doesn’t understand the science of packaging, you may have problems.’
Take the example of catheters, one of the most packaged devices around the world. ‘The packaging is critical because it has to take account of the way the catheter is sterilised, whether it uses ethylene oxide or some other gas,’ Spitzley says. ‘The questions the packaging engineer has to ask are: What are the materials? What are the effects of sterilisation? What are the customer requirements? What does the package contain?’
The range of devices that have to be packaged means that the packaging engineer has to be alert to what is being packaged. ‘If the device contains electronics, it is difficult to irradiate it,’ Larsen points out. ‘Also the engineer has to understand that it may not be possible to sterilise devices which have a biological element that way.’
Medical packaging machinery has also advanced. Sophisticated processing equip-ment with state-of-the-art controls, data acquisition systems and in-line printing capabilities are now the rule.
Global standards
The year 2005 is likely to go down as the year in which global standards were finally achieved. ‘ISO members and the European Committee for Standardisation [CEN] are harmonising their standards on the basis of ISO 11607,’ Spitzley says. ‘This should be done by September or October 2005, once the ISO has balloted all its members.’ The EU has already made its standard a requirement. The Japanese medical industry is also looking on with interest and is likely to adopt the ISO standard. Larsen stressed that both the ISO and EU are harmonising upwards, taking the higher standard, rather than seeking the lowest common denominator. The new ISO document will mean that there will be a single global standard for medical device packaging
Future developments
Among the major developments packagers expect soon are the introduction of visible barcodes and radio frequency identification (RFID) devices in packaging, which will help the supply chain to operate more efficiently. Visible bar codes, in particular, are likely to become far more prevalent. Bar coding will allow the manufacturer to keep track of their inventory and print only the label in the language of the destination market.
Some packaging professionals argue that the differences between medical device packaging and pharmaceutical packaging will blur. They point out that both industries need to protect their products from tampering.
The big difference, however, is that there is a big and growing over-the-counter business in pharmaceuticals, while there is not much of one in medical devices. Over the past ten years, more and more drugs have been sold directly to patients, although hospitals and clinics remain the main markets for medical devices.
Predictive engineering tools such as design simulation software will also help packaging designers. This allows engineers to simulate the effects of the distribution system, which is now often much longer, since devices are manufactured in locations far away from their final markets. Packagers need to be able to predict what the physical and climatic stresses are.
Printing now encompasses far more than just labelling. Bar codes are printed, and there are emerging standards for their quality because they have to be read correctly by a range of scanners.
Besides bar codes, RFID is being introduced. This technology uses a tag that contains more information than a bar code. The technology has been around since the 1980s but is only now becoming widespread in the packaging industry as an addition to barcoding.
One problem with bar codes is that they have to be printed to a high standard each time for a scanner to read the information. Tags are easier to manufacture accurately. They can also be read for a greater distance and in circumstances (such as darkened or sealed chambers) where bar codes are illegible.