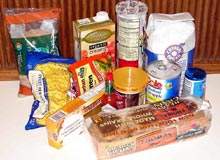
Innovation across the packaging industry is moving at a rapid rate, but keeping up with new ideas and hot topics can be tough for industry decision-makers spanning across so many vertical sectors.
In the run up to the PACE USA forum, organised by Arena International, we take a look at two key areas affecting manufacturing sustainability and weight reduction and look at how large global companies are using innovative methods to produce packaging technology to meet these needs.
Packaging sustainability is key
Biodegradable products derive from living organisms including cellulose, starch, proteins and peptides. These materials are used to create biodegradable plastics which are easily compostable to water, CO2 and residual organic carbon (compost) leaving the least amount of harmful residue behind as possible. There are two main types of biodegradable plastics on the market: hydro-biodegradable plastics (HBP) and oxo-biodegradable plastics (OBP).
The natural polymer starch is widely used and can be processed directly into a bioplastic. Many manufacturers use modified starch to overcome the problem of swelling in water, modifying it into a different polymer and chemically treating it to form polylactide (PLA). While this material is used for products such as plant pots and disposable nappies, PLA is more expensive and has not gained widespread use.
Another way of making biodegradable polymers involves getting the bacteria to produce granules of a plastic called polyhydroxyalkanoate (PHA) within its cells. Bacteria are grown in culture and the plastic is then harvested. Scientists have now taken genes from this kind of bacteria and stitched them into corn plants, which then manufacture the plastic in their own cells.
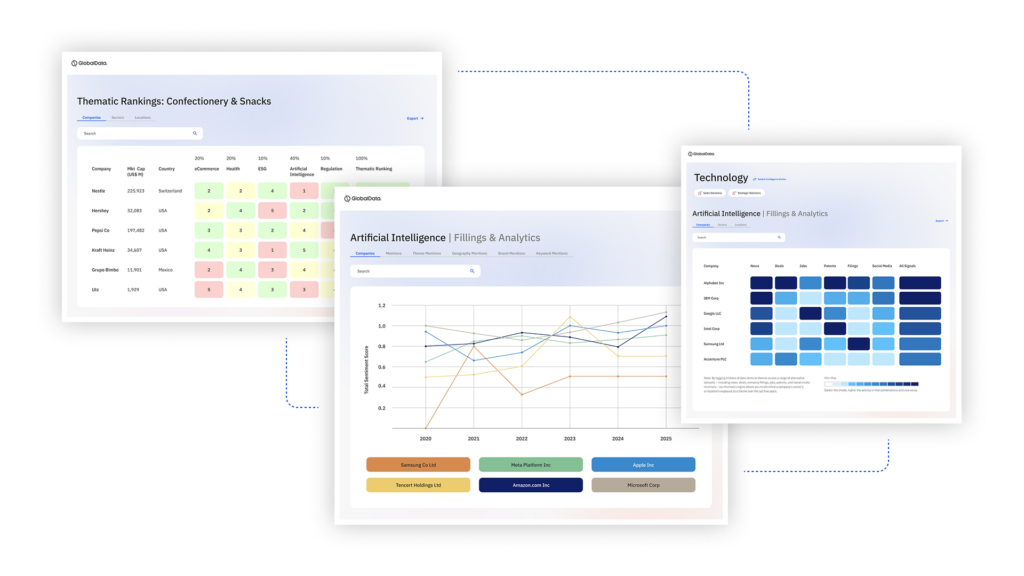
US Tariffs are shifting - will you react or anticipate?
Don’t let policy changes catch you off guard. Stay proactive with real-time data and expert analysis.
By GlobalDataScottish company Biobag, which describes itself as the world’s largest 100% biodegradable and compostable bags and films brand, uses compostable bioplastic materials based on starch and vegetable oils. The company says it does not use polyethylene to ensure the products are completely ecofriendly.
In addition to plastics bags, the plastic bottles market has also exploded in recent years. A new study by the US PET Resin Association shows that PET bottles offer a better environmental footprint than aluminum cans or glass bottles. The association claims this is achieved through the use of less energy, less solid waste generation and the creation of fewer greenhouse gas emissions.
A study by Franklin Associates for PETRA, compared total energy, solid waste and greenhouse gas emissions per 100,000oz of soft drinks packaged in typical 20oz PET bottles, 8oz bottles, and 12oz aluminium cans.
The PET bottles showed appreciably lower numbers in all areas. This included fewer greenhouse gas emissions for PET bottles, which registered 59% less than aluminium and 77% less than glass.
As well as considering the environmental footprint by using certain materials, packaging manufacturers must also reduce packaging weight to ensure legislation and consumer demand for smaller and easy-to-use packaging is met.
Lightening packaging weight
Food manufacturers have had to make rapid decisions in the last few years to keep pace with legislation by reducing packaging weights and volumes. One such company is confectionary specialist Nestlé. Easter egg packaging is a good case in point. In the last year, the company replaced non-recyclable packaging in the majority of the 25 million Easter eggs it produces. The company is one of many chocolate manufacturers reducing packaging weight and volume across all its ranges.
Nestlé is not the only major company to make big strides in reducing its packaging quantity. US fast food giant Burger King, which recently featured on packaging-gateway.com, has also targeted cost cutting. The company says it has come up with a number of innovations using the principle of “lightweighting” across its packaging business. For example, it was the first in the US to introduce recycled paper for children’s cold cups and food bags.
The alcohol industry is also significantly reducing the size and weight of its bottles. There is still however still some way to go before lightweighting is adopted by all alcoholic beverage makers.
According to the UK-based Wine and Spirit Trade Association, the industry can still do more. In 2006, recycling body WRAP launched its Container Lite project, which set out to prove that container weight can be reduced significantly by a combination of re-design or lightweighting an existing design without affecting consumer expectation, container performance or market share. WRAP is currently working with the international wine sector to encourage the lightweighting of glass containers to reduce tonnage of glass waste.
The alcohol industry offers just one example of the effort being made to cut packaging weights and volumes to meet global waste reduction targets and serve the growing expectations of consumers and environmental groups to send less waste to landfill. Researchers have worked tirelessly to incorporate cost-effective biodegradable products into the supply chain, retailers and supermarkets have cut the use of plastic bags to meet consumer demands.
Representatives from some of the biggest global corporations across the food, beverage, pharmaceutical and other industries are currently preparing to reveal more scientific breakthroughs and new technology for use across the entire packaging supply chain at PACE USA, which takes place 13-16 May 2010 in Miami, US.