
According to recently released data from the Robotic Industries Association (RIA), the first half of 2010 has marked a dramatic revival for robotics manufacturers after the worrying sales plunge that characterised 2009. North American robotics companies enjoyed a 40% surge in unit orders during the first half of 2010, with 6,316 robots (valued at $411.4 million) sold in June alone.
RIA president Jeff Burnstein was reassured by the news. “We still have a long way to go before the industry is back to pre-recession sales levels, but I’m very encouraged that we’re headed in the right direction,” he told RIA-sponsored site Robotics Online at the beginning of August 2010.
The rise is good news not only for the economy as an indicator of companies’ improved cash flow and willingness to make substantial upfront investments into technology, but also for robotics, a progressive industry that is gaining footholds in an ever-widening range of markets, including medicine and life sciences, food processing and consumer goods.
While robots are gradually infiltrating many surprising areas of our everyday lives, automation has a well-established history with the packaging industry. The tireless productivity and adjustable precision of industrial robots is a natural fit for an industry in which accuracy and speed are paramount.
Whether for delicate pick-and-place applications where robots can outpace the quickest human labour or heavy palletisation operations, automation looks to be the way forward in the long-term. Here we look at some of the most impressive recent advances in packaging robotics and highlight the benefits that robots can bring to a packaging operation.
Robotic palletisation
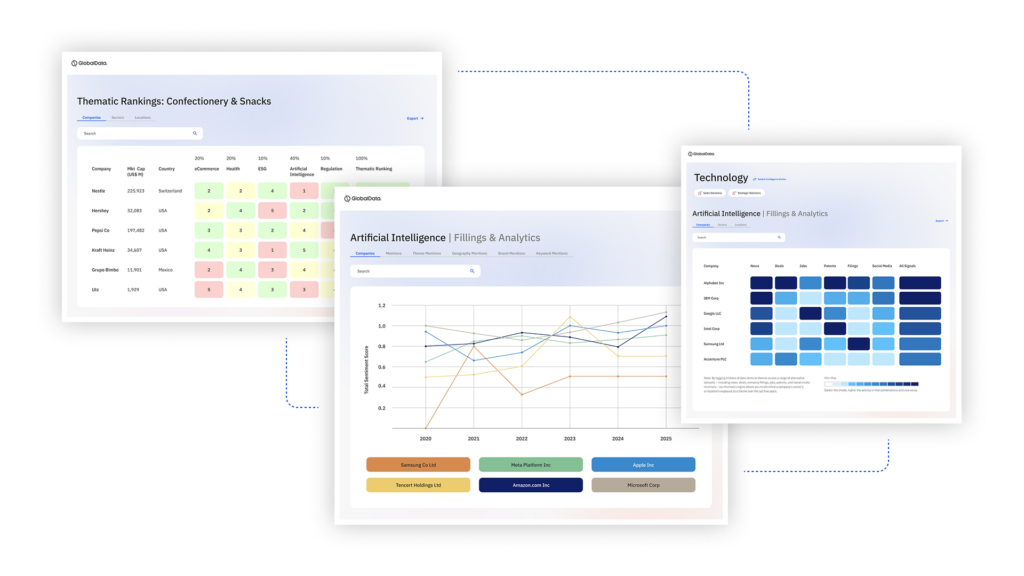
US Tariffs are shifting - will you react or anticipate?
Don’t let policy changes catch you off guard. Stay proactive with real-time data and expert analysis.
By GlobalDataRobots make a compelling alternative to both manual labour and conventional palletising machinery. Robots take up less floor space than most equivalent machines, are more efficient and cost effective than human operators, and are flexible enough to adapt to specific packaging applications without lengthy and costly reworking.
Robotic units also have the potential to dramatically improve productivity when compared with their human counterparts. At a Charwood Foods pizza processing plant in the UK, operators decided to automate the palletisation of prepared pizzas after a second production line was added. They installed a Motoman SP100X palletising robot to pack pizzas with 12 different box sizes. The robot, which palletises and secures 320 cases an hour, 24 hours a day, has been a great success for the plant. Motoman has also developed a version of the SP100X that can operate in sub-zero freezer conditions.
A new project, co-sponsored by the National Institute for Standards and Technology, the Georgia Institute of Technology and the Institute of Electrical and Electronics Engineers, could help point the way to new standards of efficiency for robotic palletisation. Called the virtual manufacturing automation competition (VMAC), the project is challenging expert teams to design automatic palletising protocols, using a virtual shop-floor space, to palletise a set number of mixed boxes as quickly as possible. The aim of the project is to establish an internationally recognised benchmark for efficiency, which should make it significantly easier for plant operators to judge the performance of palletising robots.
Robotic pick-and-place applications
Robots can provide similar advantages when it comes to the more intricate task of pick-and-place and material handling. Robotic arms can be programmed to achieve the same pick-and-place results every time, as well as being programmable when needed. There are a range of grippers in use on industrial robots depending on the fragility of handled material and the specific functions required. For more sturdy materials, hard jaws provide power and precision, but soft jaws are more flexible and suited to a range of more delicate tasks. Grippers can be powered electronically, hydraulically or pneumatically, and the range of grip methods includes vacuum,mechanical, magnetic and friction.
One of the most promising advances in pick-and-place robotics is the rise of vision-assistance. Fanuc Robotics introduced robots inbuilt vision systems that were integrated with robotic controllers in 2006. This technology allows pick-and-place robots to compensate for conveyor belt inconsistencies for maximum reliability, while the integrated controller makes set-up easy for the operator. Some criticisms have been levelled at vision-assisted robots, however, due to their high cost and the fact that vision technology has not yet achieved the processing speed necessary for the most high-end applications.
When speed is of the essence, industrial pick-and-place units have made significant strides in recent years, pushing the threshold of cycles per minute (the standard measure for the speed of industrial robots) ever further.
In late 2009, the Quattro s650H parallel robot, named after the unique four-arm kinematic that facilitates its speed and acceleration, became the first industrial robot to break 300 cycles a minute on a standard pick-and-place cycle. Rush LaSelle, sales and marketing director for manufacturer Adept Technology, believes the robot provides the best of both worlds for customers.
“As Adept continues driving technology to higher levels of performance, our clients benefit by realising throughput previously only offered by conventional equipment combined with the flexibility of manual labour,” he says. Adept have also released a variant of the Quattro, the s650HS, that has been approved to handle raw meat and poultry by the US Department of Agriculture, making it an ideal choice for meat packaging.
Robots learning the soft touch
Robots are not simply used for their brute strength and speed, however. As costs fall, increasingly sophisticated technology can be feasibly incorporated into packaging robots. Automation can now be relied upon for even the most delicate duties.
The IRB340 Flexpicker, manufactured by ABB, is capable of handling and packaging the most delicate materials. At the main plant of Swedish cracker company Wasabröd, the Flexpicker stacks 90 crackers a minute with high availability and low waste, helping the company to satisfy demand by increasing output from 7.7t to 38.5t in just two years. Wasabröd head of production Per Inge Eriksson told the press that the robot had increased productivity on its fragile cracker sandwich line by 10%.
Robotics is truly representative of the future of the packaging industry. Although the initial investment has proven intimidating for some plant operators, companies are increasingly waking up to the fact that with their productivity, reliability and lower ongoing costs, robots offer a good return on investment even in the most severe economic conditions.