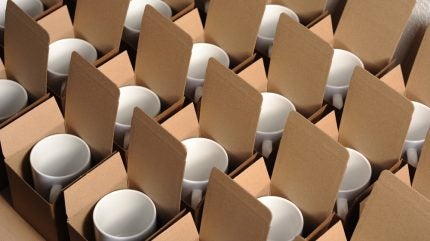
Additive manufacturing, commonly known as 3D printing, is transforming the way products are designed, produced, and distributed. As this technology advances, the need for specialised packaging tailored to 3D printed goods has grown significantly.
Unlike traditional products, items produced through additive manufacturing often have unique shapes, delicate features, or are made from unconventional materials.
This creates new challenges and opportunities in the packaging industry, prompting innovation to protect and preserve these products throughout their supply chain.
Understanding the unique packaging needs of 3d printed goods
3D printed products can vary widely—from prototypes and medical devices to customised consumer goods and aerospace components. Each type has distinct packaging requirements.
The complexity of shapes and materials used means standard packaging solutions may not offer sufficient protection. For example, brittle materials like certain resins or ceramics need cushioning to avoid damage, while intricate geometries may require custom-fit supports.
Packaging for additive manufacturing must also consider the potential for sensitive surface finishes, which can be scratched or degraded by conventional packing materials.
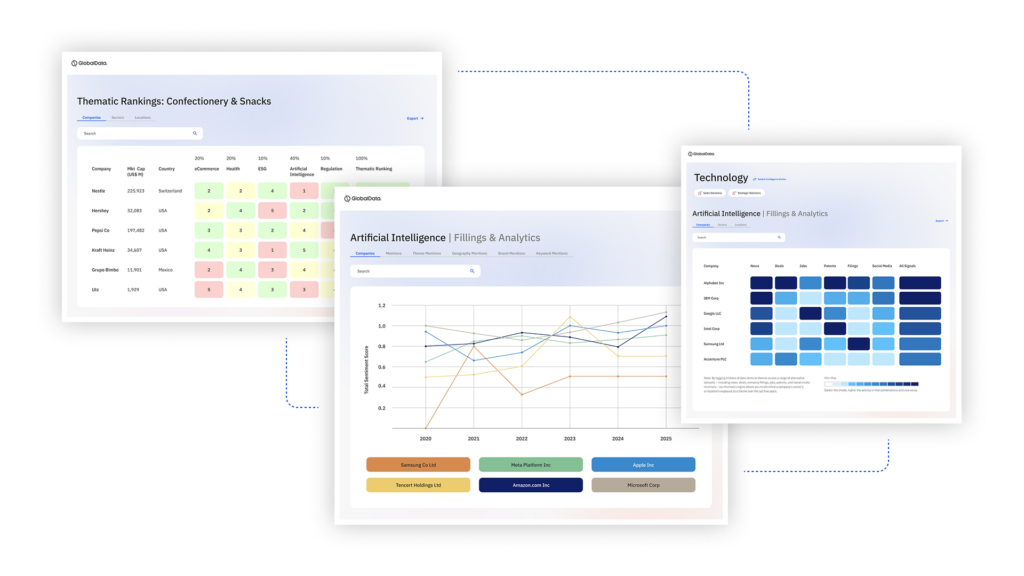
US Tariffs are shifting - will you react or anticipate?
Don’t let policy changes catch you off guard. Stay proactive with real-time data and expert analysis.
By GlobalDataMoreover, some 3D printed items are produced in small batches or even as one-offs, making cost-effective packaging solutions vital for economic viability.
The ability to protect the product during transit, storage, and handling while maintaining a compact footprint is essential for the sustainable growth of this sector.
Materials and design innovations in packaging for additive manufacturing
To meet these challenges, packaging designers are exploring a range of innovative materials and designs tailored to the unique properties of 3D printed goods.
Foam inserts made from biodegradable or recyclable materials can be custom-cut to cradle delicate parts, ensuring stability and shock absorption.
Flexible packaging solutions, such as air-filled cushions or moulded pulp, also provide effective protection without adding significant weight.
Another key trend is the use of modular packaging components that can be easily adapted to different product sizes and shapes. This flexibility reduces waste and lowers costs, aligning with broader sustainability goals.
Some companies are even utilising 3D printing itself to create bespoke packaging inserts, perfectly contoured to the product, which can be produced on-demand and reused or recycled.
Sustainability remains a major focus, with many manufacturers seeking packaging that is both protective and eco-friendly.
This involves selecting materials with a lower environmental impact and designing for minimal waste, ensuring that packaging complements the innovative nature of additive manufacturing rather than detracting from it.
Challenges and future directions in additive manufacturing packaging
While the packaging industry is adapting to the needs of 3D printed goods, several challenges persist.
One significant issue is the lack of standardisation in additive manufacturing processes and materials, which makes it difficult to create universal packaging solutions. This variability requires packaging to be highly customisable, sometimes resulting in higher production costs.
Temperature sensitivity is another concern. Some 3D printed materials can be affected by heat or humidity, necessitating climate-controlled packaging or special barrier materials to maintain product integrity.
For medical or aerospace components, strict regulatory requirements also influence packaging design, demanding traceability, sterilisation compatibility, and tamper evidence.
Looking ahead, advances in smart packaging technologies may play an important role in supporting additive manufacturing. Embedded sensors could monitor environmental conditions during transit, alerting users to any risks of damage or contamination.
Interactive packaging might also provide product information or authenticity verification, enhancing the value chain.
As 3D printing technology continues to evolve, packaging solutions will need to keep pace, combining protection, adaptability, and sustainability.
Collaboration between additive manufacturing experts and packaging engineers will be key to developing innovative, cost-effective solutions that ensure products reach customers in optimal condition.