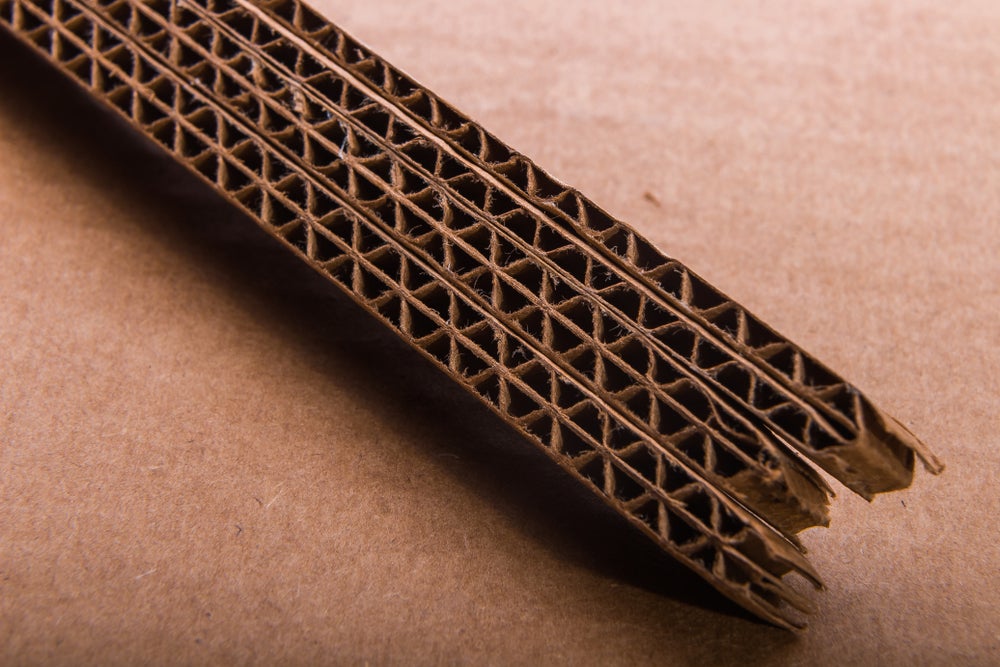
Multilayer packaging recycling refers to the process of recycling packaging materials that are made up of multiple layers of different materials such as plastic, aluminium and paper.
While recycling single-layer materials like cardboard or plastic bottles is relatively straightforward, multilayer packaging poses enormous challenges.
Overcoming these obstacles requires collaboration among packaging manufacturers, recycling facilities, governments and consumers, focusing on innovative technologies, improved sorting methods, standardised processes, creating market demand for recycled materials and supportive policies.
Breakthrough collaboration: multilayer packaging successfully recycled on industrial scale
A ground-breaking collaborative project involving BASF, Krones, Südpack and Tomra Recycling Sorting has successfully demonstrated that multilayer packaging made of PET can be recycled on a large scale using existing recycling infrastructure.
This is significant because recycling multilayer packaging has always been a challenge.
In the first trial at a Krones pilot plant in Flensburg, Germany, the companies were able to completely separate the PET and polyethylene (PE) layers in the multilayer packaging in 69% of the cases, with an additional 12% partially separated.
The project involved major companies from different parts of the plastics and recycling industry, which provided valuable insight into the difficulties of recycling multilayer packaging.
Phase one: sorting and debonding
The first phase of the project, carried out in 2021, involved sorting trials by Tomra using PET/PE trays manufactured by Südpack. These trays were made with a special adhesive developed by BASF. Südpack, with its expertise in lamination, created PET/PE films that could be separated by hot washing. The company specialises in producing high-performance packaging films for various products.
Tomra’s near-infrared Autosort technology was used to sort the recyclable multilayer packaging from a mixture of recyclable and non-recyclable trays. The NIR sorting equipment successfully detected the multilayer trays made with BASF’s adhesive, showing that they can be sorted for recycling.
In the second phase, Krones conducted trials to separate the laminated PET/PE films into single layers on an industrial scale. Krones sells equipment for washing and decontaminating PET packaging for recycling.
The separation was done using a standard hot-washing process commonly used for PET recycling. The process was successful, resulting in reusable PET and PE that could be used as separate materials.
The separated materials were recycled using existing mechanical recycling technology. Depending on the packaging application, either mechanical or chemical recycling could be used.
Mechanical and chemical recycling possibilities
Initial tests showed that the mechanically recycled PET could be reused for food-contact applications, but chemical recycling would be required for the recycled PE to be used in food packaging. Further tests will be conducted to explore this possibility.
BASF’s water-based Epotal adhesive played a crucial role in enabling the easy separation of PET and PE layers without compromising the adhesive strength. The collaboration partners are working on optimising the process to improve the recycling rate by adjusting parameters and adhesive qualities.
The collaboration between BASF, Krones, Südpack and Tomra is ongoing, with a focus on improving the recycling rate and the quality of recycled materials.
The project aims to stimulate a broader discussion within the industry to implement multilayer recycling in the future.
This innovative process for recycling multilayer packaging aligns with the European Commission’s Packaging and Packaging Waste Regulation, which requires most packaging to be recyclable by 2030 in the EU.