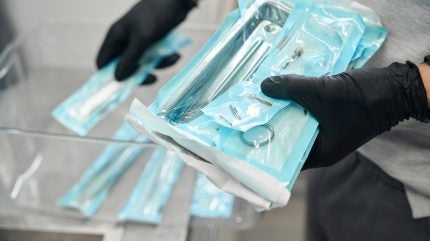
Medical device packaging plays a crucial role in the healthcare industry by protecting sensitive equipment and ensuring patient safety.
Whether it’s a surgical instrument, implant, or diagnostic tool, packaging must preserve the device’s sterility, prevent contamination, and facilitate safe handling.
Discover B2B Marketing That Performs
Combine business intelligence and editorial excellence to reach engaged professionals across 36 leading media platforms.
With increasing regulatory requirements and advances in materials, medical device packaging has become a specialised field that combines innovation with strict standards.
The importance of sterile and protective packaging
Medical devices often require sterile conditions to avoid infections and complications during use. Packaging serves as a primary barrier, maintaining sterility from the manufacturing site to the point of use.
This involves using materials and designs that can withstand sterilisation methods such as steam, ethylene oxide, or radiation without compromising the device’s integrity.
Protection goes beyond sterility. Packaging must shield devices from physical damage like impacts, moisture, dust, and temperature fluctuations during transport and storage. For fragile devices such as catheters or electronic monitors, cushioning and robust outer layers are essential.
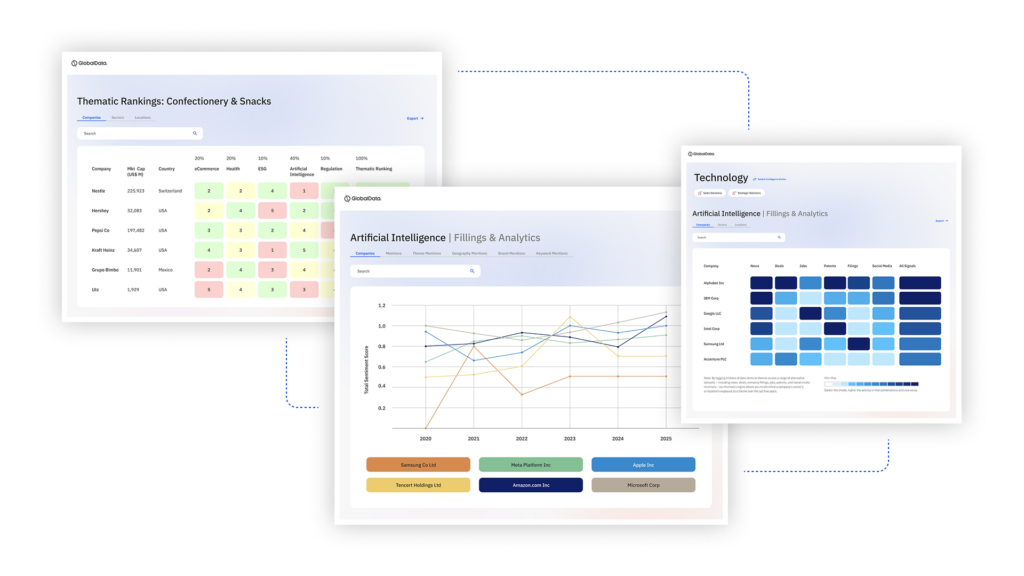
US Tariffs are shifting - will you react or anticipate?
Don’t let policy changes catch you off guard. Stay proactive with real-time data and expert analysis.
By GlobalDataThe packaging design also needs to enable easy opening by healthcare professionals without risking contamination, often featuring peelable seals and tamper-evident features.
Materials and technologies in medical device packaging
Choosing the right materials is key to effective medical device packaging. Common options include medical-grade plastics, such as polyethylene and polypropylene, as well as paper-based materials that meet cleanliness and biocompatibility standards. Laminates combining plastic films with foil or paper can offer superior moisture and oxygen barriers.
Innovations are also shaping the industry. For instance, peelable film seals now allow sterile access without scissors or knives, reducing injury risks. Active packaging solutions, incorporating antimicrobial layers or humidity control agents, are emerging to further protect sensitive devices.
Sustainable materials are gaining attention, with manufacturers seeking recyclable or biodegradable packaging to reduce environmental impact while still meeting regulatory demands.
Sterilisation compatibility is another important factor. Packaging must withstand sterilisation without degrading or releasing harmful substances. This means extensive testing to confirm materials retain strength and barrier properties after exposure to sterilising agents.
Regulations and quality assurance in packaging
Medical device packaging is tightly regulated to guarantee safety and compliance. In Europe, the Medical Device Regulation (MDR) outlines packaging requirements alongside device performance standards.
Similarly, the US Food and Drug Administration (FDA) provides guidelines ensuring packaging integrity and sterility maintenance.
Manufacturers must perform rigorous validation processes, including packaging design, materials testing, and sterilisation validation.
Quality assurance systems track packaging throughout production, verifying sealing strength, cleanliness, and shelf life. Traceability is crucial, allowing defective packaging or devices to be quickly identified and recalled if necessary.
Labelling requirements also form part of the packaging regulations. Clear, legible information such as lot numbers, expiry dates, and handling instructions must be present to support safe use.
Some packaging now incorporates QR codes or RFID tags for digital tracking and authentication, enhancing inventory management and counterfeit prevention.
Looking ahead
Medical device packaging is an essential component in delivering safe and effective healthcare products. Its role in maintaining sterility, protecting devices, and ensuring regulatory compliance cannot be overstated.
Advances in materials and technology continue to enhance packaging performance, while sustainability considerations are increasingly influencing design choices.
For healthcare professionals and manufacturers alike, understanding the complexities of medical device packaging is vital to safeguarding patient health and supporting medical innovation.