
UK-based natural plastics producer Biome Bioplastics has partnered with compostable packaging films maker Futamura to present a range of bio-based and compostable multilayer films.
The films combine Biome’s biodegradable sealant resins with compostable NatureFlex cellulose films from Futamura to generate various laminated flexible structures.
Biome Bioplastics sales manager Myriam Moeyersons said: “This range of multilayer films allows brand owners to move away from non-recyclable packaging and show that they are at the forefront of the drive to create a circular economy for plastics.
“There is no time to lose if we are to bear down on packaging waste and achieve the aims of the UK Plastics Pact. We must immediately start implementing changes to existing packaging.”
According to the company, the compostable films are compliant to the European industrial composting standard EN13432 and are capable of disintegrating up to 90% within 12 weeks.
The packaging films maker also tested the materials and determined that they are non-toxic to both soil and plant life.
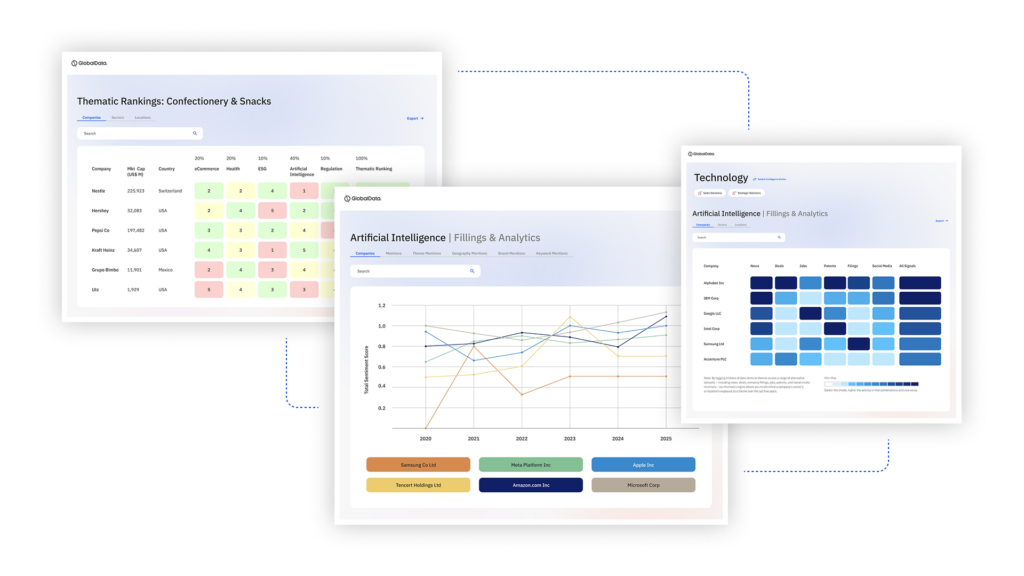
US Tariffs are shifting - will you react or anticipate?
Don’t let policy changes catch you off guard. Stay proactive with real-time data and expert analysis.
By GlobalDataFutamura product and sustainability manager Lucy Cowton said: “Futamura chose to partner with Biome as our companies are aligned in their passion to produce technically strong, sustainable and compostable alternatives to conventional packaging films.
“Biome’s sealant resins are an excellent pairing because they complement the heat resistance and barrier properties of our NatureFlex range with their puncture resistance and strong sealability.”
The firms have demonstrated that the films can offer good oxygen and moisture barrier properties, as well as efficient sealability.
They are suitable for conventional and digital printing processes, enabling manufacturers to enhance their branding.