Speciality chemicals firm Clariant, together with its Healthcare Packaging division, has launched a new line of desiccants for bulk pharmaceuticals.
The introduction of the Sorb-It PHARMA desiccant bags adds to Clariant’s existing pharmaceutical desiccant products, including packets and canisters that are used in finished drug product containers.
Recently, the company invested in a new ISO 15378 GMP certified facility at its plant in Belen, New Mexico, US, for the production of the new line of desiccants.
The company noted that Sorb-It PHARMA is being produced at the facility to meet global standards for primary pharmaceutical packaging.
Clariant Healthcare Packaging product manager Mark Florez said: “The introduction of Sorb-It PHARMA desiccant bags marks a final milestone in Clariant’s plan to produce its pharmaceutical desiccant lines in ISO 15378 certified production environments.
“ISO 15378 is globally recognised by the pharmaceutical industry, and it is important that we offer our full range of products accordingly.”
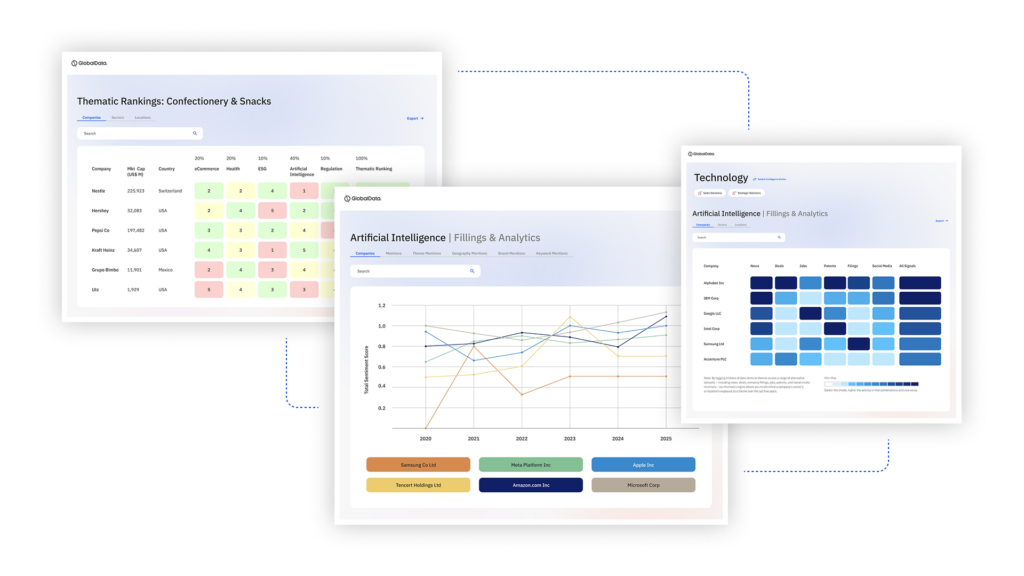
US Tariffs are shifting - will you react or anticipate?
Don’t let policy changes catch you off guard. Stay proactive with real-time data and expert analysis.
By GlobalDataFilled with silica-gel desiccant, the Sorb-It PHARMA desiccant bags are designed to provide protection to bulk drugs, finished drugs during transport and storage, active pharmaceutical ingredients (APIs), and work-in-process. They are available in a range of standard sizes of 50g, 100g, 200g, 250g, and 400g.
The company noted that the new desiccant bags adhere to US Pharmaceopeia USP testing requirements for auxiliary packaging components.
In an effort to meet the business continuity planning (BCP) requirements of global pharmaceutical and healthcare customers, Clariant is not limiting the production of the Sorb-It PHARMA desiccant bags to New Mexico. Production will also be carried out at the company’s sites in Dongguan, China and Romorantin, France.