
Austria-based Greiner Packaging (Greiner) and its industry partners have found a new way to manufacture polyethylene terephthalate (PET) cups using 100% recycled material via an injection-moulding process.
Greiner’s industry partners include mould maker Brink BV (Brink) as well as Engel, a manufacturer of injection-moulding machines.
The latest development comes after an intensive development phase, under which the companies leveraged injection-moulding technology to produce new thin-walled, sealable cups that are suitable for filling lines.
The new cups are made of recycled polyethylene terephthalate (rPET), which has the potential of reducing the overall carbon dioxide equivalent (CO₂e) emissions compared to its virgin plastic equivalent and will contribute toward a circular economy.
Greiner Global Product Group manager Sebastian Diensthuber said: “When developing the thin-walled, injection-moulded cups made of PET, it was particularly important for us to develop a solution that was not only innovative but also able to withstand our customers’ industrial requirements.
“The cups we developed together with Brink and Engel are designed in such a way that a transition to the new generation of cups is possible, both in filling and sealing.”
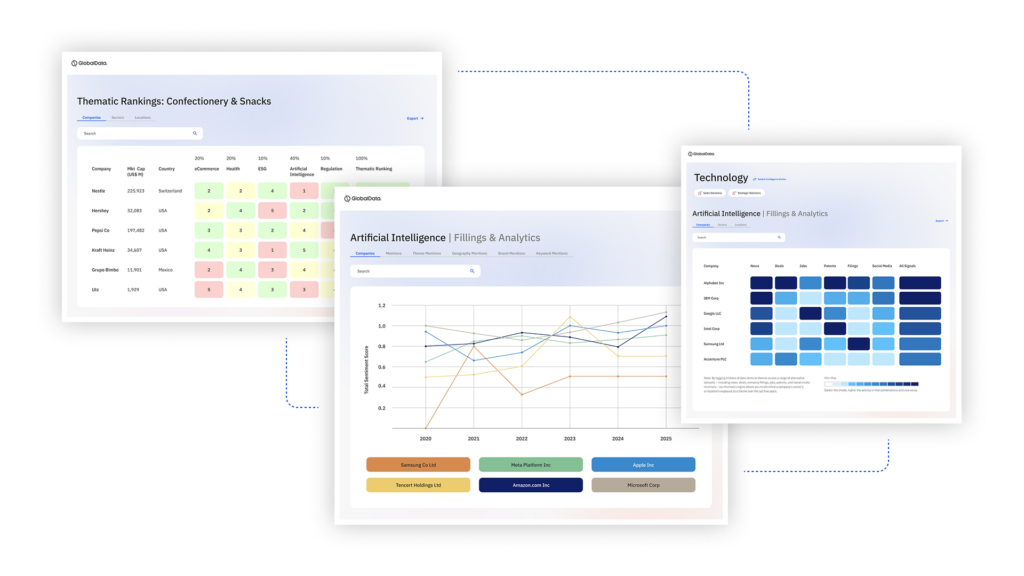
US Tariffs are shifting - will you react or anticipate?
Don’t let policy changes catch you off guard. Stay proactive with real-time data and expert analysis.
By GlobalDataThe new cups are optimally recyclable, adhere to legal standards, are lightweight in nature and are suitable for industrial purposes.
Greiner explained that until now PET was mainly being used for thermoforming applications, and if PET was used in injection-moulding, it would be exclusively used on cans, not cups.
Previously, such thin-walled cups were only made up of polypropylene material, which has not received positive feedback from the European Food Safety Authority.
With the use of these injection-moulded cups, the packaging industry will have wider options, especially in terms of food packaging, says Greiner.
Greiner claimed that the production of cups using an injection-moulding process will further maintain the uniform thickness of walls, due to an even distribution of plastic in the mould during the process itself.
The cups can also be decorated through an in-mould labelling method.