German packaging systems supplier KHS and US-based automation equipment provider Agr International have developed the Unit Mold Control system for polyethene terephthalate (PET) bottle production.
The digital, automated process control system is connected with the KHS controller and is available as part of KHS InnoPET Blomax series to help regulate the blow moulding process at respective stations.
This improves bottle quality with lower preform weights.
KHS Corpoplast Technology head Frank Haesendonckx said: “This enables material distribution to be more precisely controlled per station, thus minimising variations in the wall thickness from mould to mould by more than 30%.”
The system’s inspection technology continuously measures the material distribution in each bottle and automatically adjusts settings for optimisation.
Haesendonckx added: “With this, system deviations in the individual mould stations are identified. By applying an algorithm, the degree of variability is reduced without operator intervention, and possible incorrect settings are avoided.”
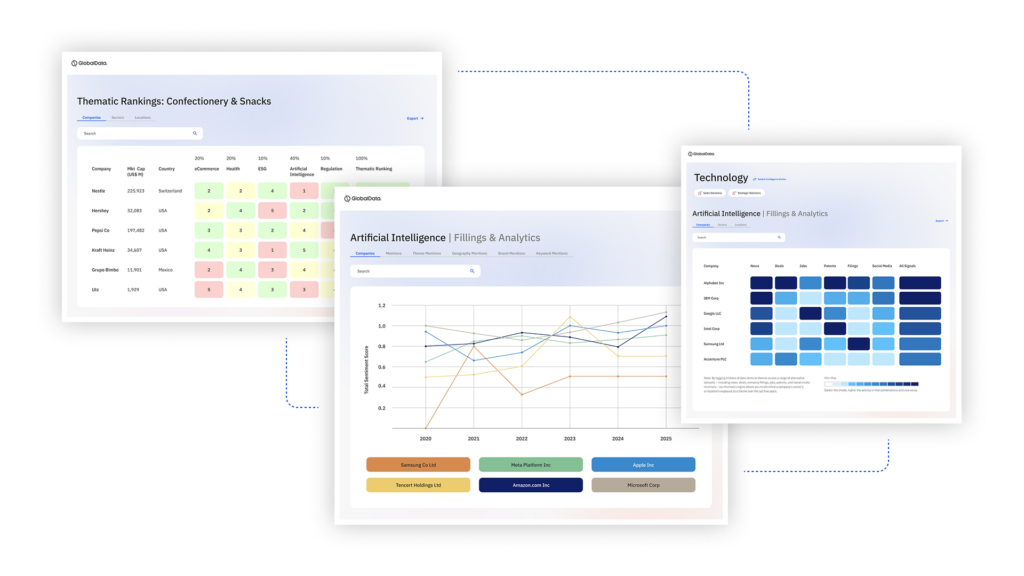
US Tariffs are shifting - will you react or anticipate?
Don’t let policy changes catch you off guard. Stay proactive with real-time data and expert analysis.
By GlobalDataKHS and Agr hold the industrial property rights of the new system.
Unit Mold Control also helps to improve bottle stability mainly with an increased percentage of recyclate content in PET bottles.
The system is available as an option for KHS InnoPET Blomax Series IV and V stretch blow moulders and can also be installed into existing plant machinery.
AGR COO Robert Cowden said: “Our commitment to the global beverage market is to provide innovative process control solutions for the factory floor.
“In doing so, we are helping to constantly optimise processes and improve production line efficiency and productivity by reducing unplanned downtime, labour content per produced container and energy costs.”