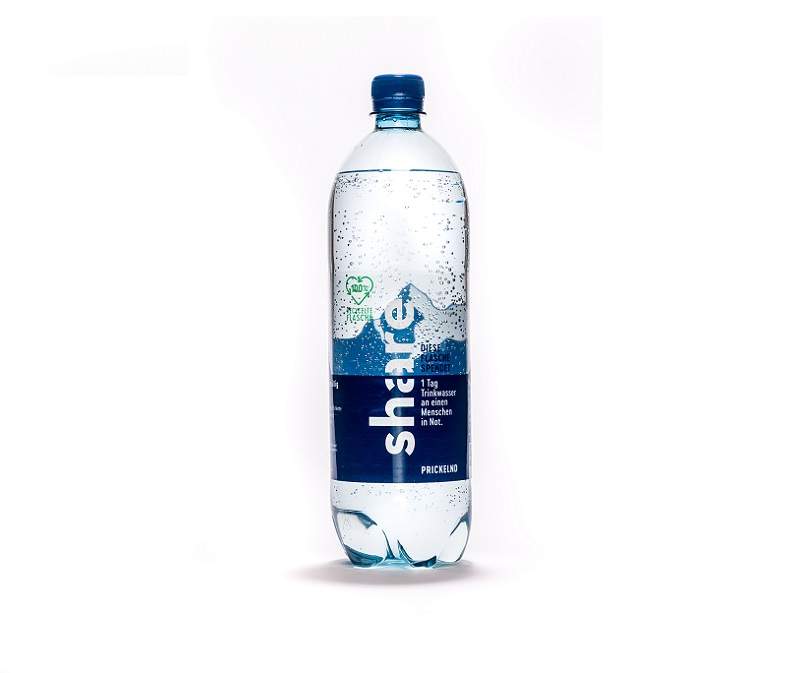
KHS Group and Germany-based beverage producer Share have developed polyethylene terephthalate (PET) bottles made of 100% recyclate.
The bottles were used to introduce Share’s new still and carbonated water lines as part of the company’s plans to put water into one million recycled PET water bottles per month in 2019.
According to Share, the plans are aimed at reducing more than 200 metric tonnes of plastic waste annually.
The packaging firm assisted Share in designing and developing the PET bottles with its expertise from the Bottles and Shapes consultancy programme.
Share used KHS technology to bottle the new water line at its Allgäuer Alpenwasser plant in Oberstaufen. The company also used an InnoPET Blomax stretch blow moulder to blow the bottles.
KHS Corpoplast Northern Europe sales lead Marc Eysel said: “We implemented the development very quickly and worked on a suitable design together.
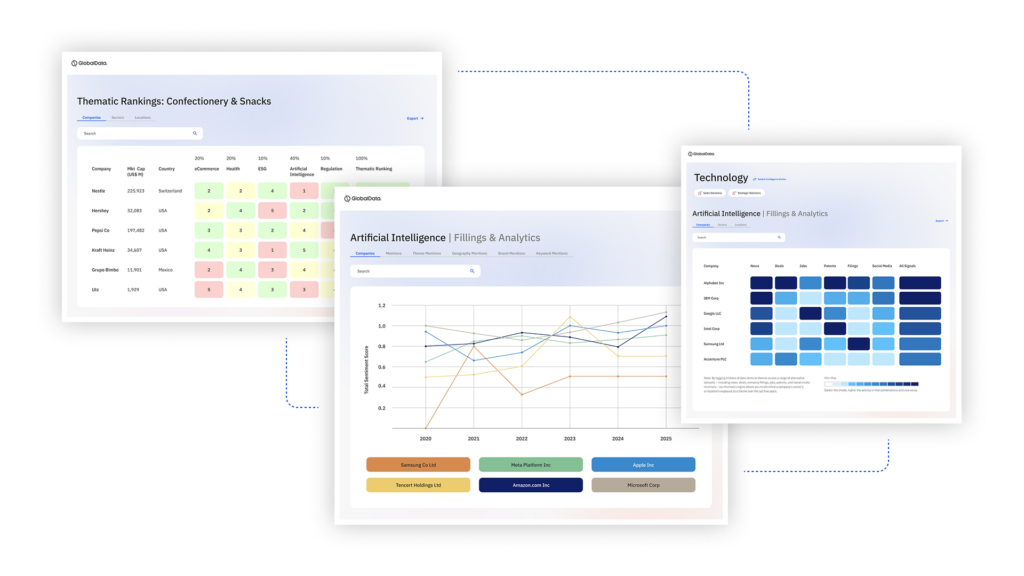
US Tariffs are shifting - will you react or anticipate?
Don’t let policy changes catch you off guard. Stay proactive with real-time data and expert analysis.
By GlobalData“Thanks to its holistic Bottles and Shapes consultancy programme, the systems supplier was able to contribute to the Share project experience drawn from over 4,000 designed bottles.
“KHS developed the bottle very quickly for us, which was enormously helpful. Manufacture is actually simpler as the material’s darker colour makes the preforms easier to heat than PET bottles made of virgin material.”
The new water line is currently available at locations of supermarket chain REWE and drug store dm across Germany.
Eysel added: “A number of bottlers wishing to increase the amount of recycled PET they use have now contacted us.
“The protection of the environment also plays an important role at KHS. We support this by providing resource-saving plant engineering and also by developing sustainable PET bottles.”
Share has also partnered with its bottler Mineralbrunnen Allgäuer Alpenwasser and preform manufacturer Plastipack for the recycled PET bottles.