
German filling and packaging systems supplier KHS has unveiled a new Innopas SX tunnel pasteuriser to offer greater flexibility to the beverage industry in the pasteurisation process.
With a modular design, the pasteuriser offers enhanced microbiological safety and serves a range of products with shorter market shelf lives.
The company, which developed the model to meet growing demands of the beverage industry, has also optimised spare part management for the flexible machine by reducing the number of components required to keep in stock and lowering the delivery times for spare and wear parts.
In the wake of the demand for flexibility in filling, the machine offers pasteurisation of filled and sealed beverage containers to ensure longer shelf lives.
Innopas SX, whose basic functionality is similar to the ‘tried-and-tested’ tunnel pasteuriser systems provided by the company, can be used for cans, glass and PET bottles.
However, the pasteurisation unit or PU control system responds variably to changes in conditions.
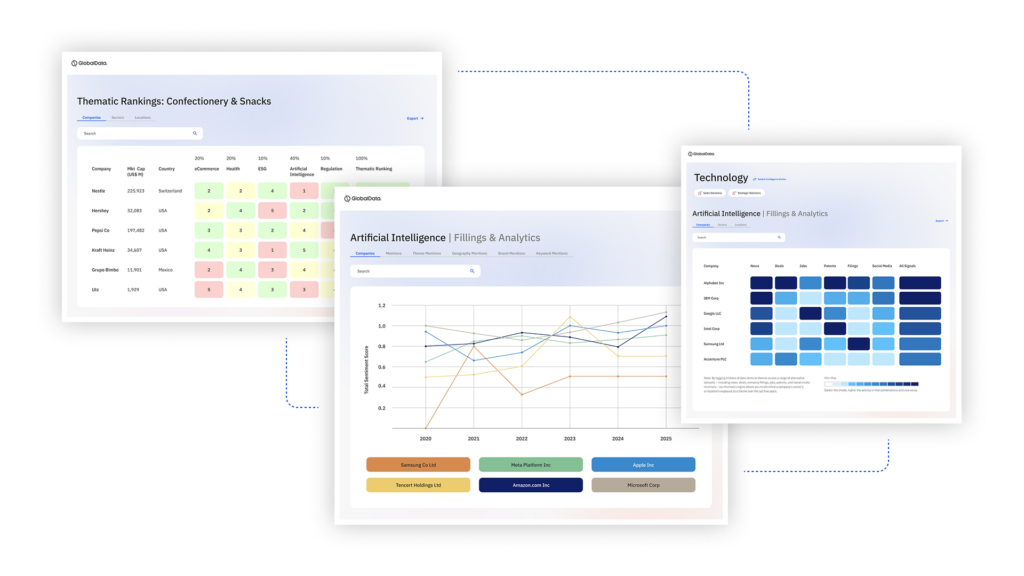
US Tariffs are shifting - will you react or anticipate?
Don’t let policy changes catch you off guard. Stay proactive with real-time data and expert analysis.
By GlobalDataExtended functions, such as optional speed regulation in the dynamic PU control system of the KHS Innopas SX, are expected to offer flexibility and savings in energy.
Based on the conveyor speed, the individual zone temperatures are automatically raised or lowered, the company noted.
KHS Bottle Washers and Pasteurizers product manager Knut Soltau said: “This allows the pasteuriser to dynamically adjust to match the line behaviour within a range of 50 to 105% of the nominal capacity for most processes without making any drastic changes to the pasteurisation units and maximum product temperature.”
The dynamic PU control helps in the regulation of the process temperatures within the hot zones of the tunnel pasteuriser, thereby allowing maximum product safety and flavour stability.
Furthermore, the new programme for PU control enables customers to independently adapt the pasteurisation unit set point for a specific container type.
Soltau added: “In this way subsequent product changes or new products can be easily made or introduced at any time. Bottlers can thus react quickly to changes on the market and product trends.”
Improvements have been made to the design of its Innopas SX to support easy operation and simplify maintenance and cleaning of the system.