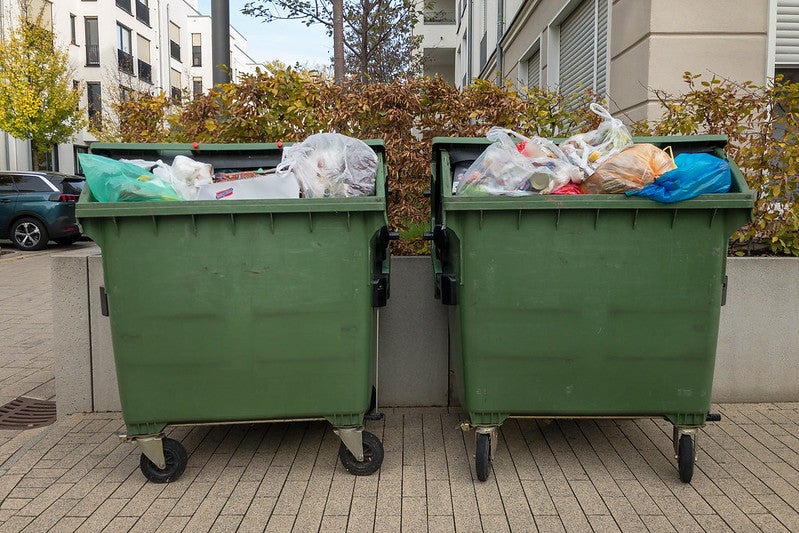
The Materials Recovery For the Future (MRFF) consortium has announced successful results in its pilot project on flexible plastic packaging (FPP) in the US.
It was conducted in partnership with J.P. Mascaro & Sons at the TotalRecycle Material Recovery Facility (MRF) in Birdsboro, Pennsylvania.
Underwritten by the MRFF, the pilot programme showed successful collection, separation and preparation for FPP recycling.
A new pilot research report titled, “Flexible Packaging Recycling in Material Recovery Facilities Pilot” has been prepared by Resource Recycling Systems (RRS).
It revealed that capturing of FPP in a single-stream MRF is possible with sufficient “supply of optical sorting capacity and peripherals”.
The resultant product after processing, called rFlex, is reusable in different markets.
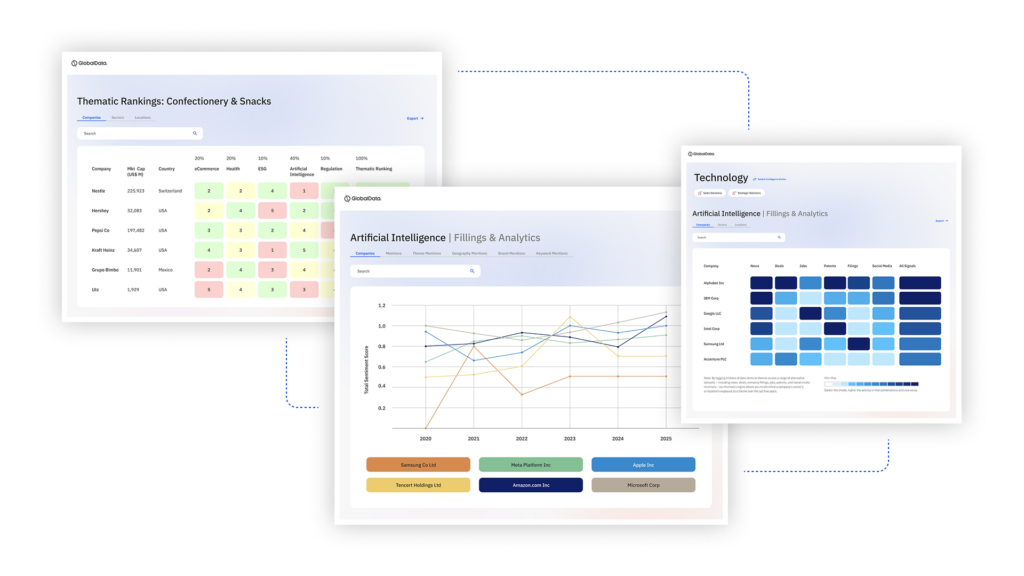
US Tariffs are shifting - will you react or anticipate?
Don’t let policy changes catch you off guard. Stay proactive with real-time data and expert analysis.
By GlobalDataMRFF Steering Committee co-chair Brent Heist said: “Approximately 12 billion pounds of FPP are consumed annually in the US, and it’s one of the fastest growing consumer packaging formats, but collecting, sorting, recycling and reintroducing this material back into the marketplace as new products requires a comprehensive approach to ensure that these materials don’t end up in landfills.”
By installing FPP sortation equipment at the TotalRecycle MRF, four of five pilot performance goals were achieved in a year. It is set to soon achieve the fifth goal.
MRFF research director and vice-president, RRS, Susan Graff said: “Our hope is that the pilot research serves as a valuable data set to help other MRFs and communities economically recycle FPP while making cleaner paper bales.”