British heat-sealing specialist Proseal has designed and installed a blueberry punnets packing system for berry and stone fruit providers Berry Gardens, in a move to increase the production speed and accuracy, as well as reduce product waste.
Proseal claims that the operations of the machine have been made more ergonomical and user-friendly.
Compliant to hygiene standards of the food industry, the machine features a Proseal GT3 tray sealer that enables production of 210 packs per minute.
It also has a twin lane conveyor that employs a continuous motion chain and peg system, which helps packs to be streamed seamlessly into the tray sealer, by increasing the pre-sealing tray accuracy.
Berry Gardens official David Perry said: "Blueberries are notoriously difficult to handle in any type of automated system.
"The Proseal system is fast and efficient, and minimises product waste, and this makes an important contribution to our ability to deliver a high-quality finished product to our customers."
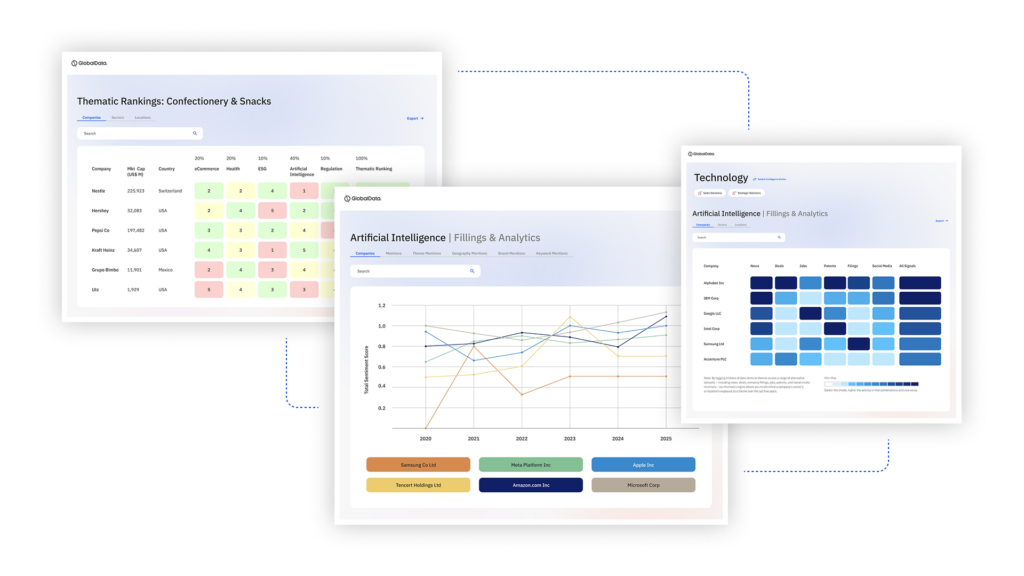
US Tariffs are shifting - will you react or anticipate?
Don’t let policy changes catch you off guard. Stay proactive with real-time data and expert analysis.
By GlobalDataThe distance between the packs and sealing heads has been reduced, which also helps in reducing wastage of the punnets.
The feed conveyor is a three-tier packing system and trays have to be grouped into rows of seven.
Boxes with unsealed punnets are delivered to packing stations along the top conveyor, which are then sent to a rack next to the middle twin lane conveyor where the packs are sealed.
Handling the machine has also become easier for the operators, as they don’t need to twist and turn during the packing operations.
An improved ‘Free-Lift’ tool loading system enables faster transfer of pre-heated tool sets to Proseal’s auto tool connection, which helps to carry out tool changes in around three minutes.