
Researchers at the Tel Aviv University in Israel have developed a process to make bioplastic polymers from microorganisms that feed on seaweed.
Scientists have produced a bioplastic polymer known as polyhydroxyalkanoate (PHA), which is biodegradable, produces zero-toxic waste and can be recycled into organic waste.
According to the United Nations, plastic is a major source of pollution in the ocean, accounting for up to 90% of pollutants found.
Tel Aviv University researcher Dr Alexander Golberg said: “Plastics take hundreds of years to decay. So bottles, packaging and bags create plastic continents in the oceans, endanger animals and pollute the environment.
“A partial solution to the plastic epidemic is bioplastics, which don’t use petroleum and degrade quickly. But bioplastics also have an environmental price. To grow the plants or the bacteria to make the plastic requires fertile soil and fresh water, which many countries, including Israel, don’t have.
“Our new process produces plastic from marine microorganisms that completely recycle into organic waste.”
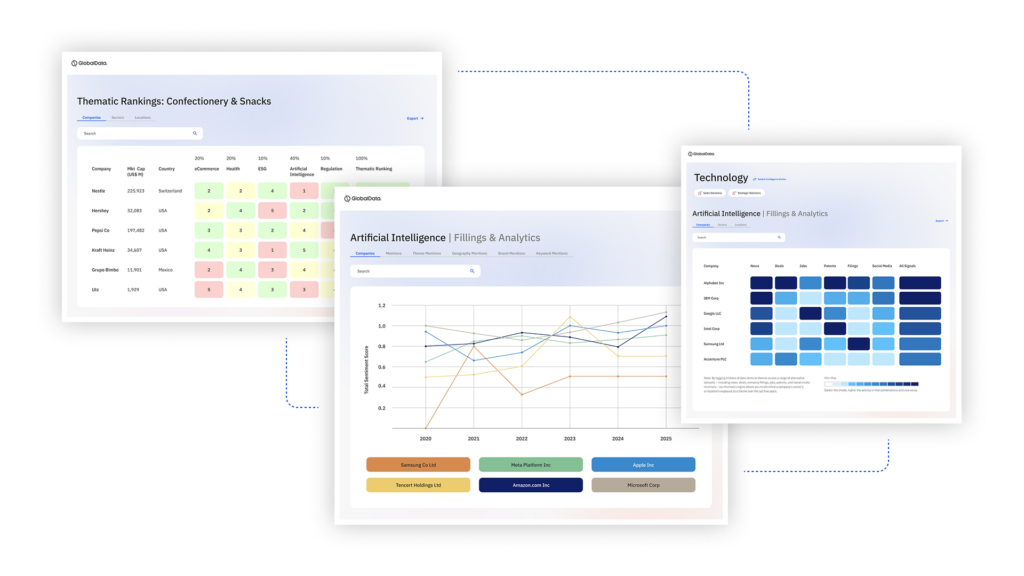
US Tariffs are shifting - will you react or anticipate?
Don’t let policy changes catch you off guard. Stay proactive with real-time data and expert analysis.
By GlobalDataGolberg highlighted that the process will not strain valuable resources such as agricultural land and fresh water that are used to grow plants for use in bioplastics. They also noted that it will be a good alternative for countries with a shortage of fresh water.
The process uses multi-cellular seaweed, which is cultivated in the sea. The microorganisms eat algae and produce a polymer that can be used to make bioplastic.
Golberg added that the team of researchers are undertaking research to find the most suitable bacteria and algae for producing polymers for bioplastics with different properties.
In July, researchers at the Georgia Institute of Technology in the US created a flexible film using crab shells and tree fibres. The researchers suggested the film as a potential alternative to flexible plastic packaging.