
US-based flexible packaging solutions provider Scholle IPN has commercialised the first-ever pre-made, sterilised spouted pouch system for aseptically-processed products.
Scholle IPN’s CleanPouch Aseptic System features a new spout, plug and cap combination, pouches made within cleanroom environments and a small-footprint, high-output aseptic rotary filler, the SureFill 100P – Aseptic.
Scholle IPN Technology director David Bellmore said: “We’ve used nearly fifty years of aseptic packaging know-how to create this new system.
“From the outset of design, finite element analysis, computational fluid dynamics, rapid prototyping and extensive testing through the prototyping phase were keys to development.
“The knowledge gained from our in-market success with the SureFill line of aseptic bag-in-box packaging has helped prove out our process and gives us the utmost confidence that this system will deliver aseptically-processed products safely, naturally, economically, and sustainably.”
The CleanPouch Aseptic System will initially be installed at Wright Foods, an aseptic food processing and co-packing company located in Troy, North Carolina, US.
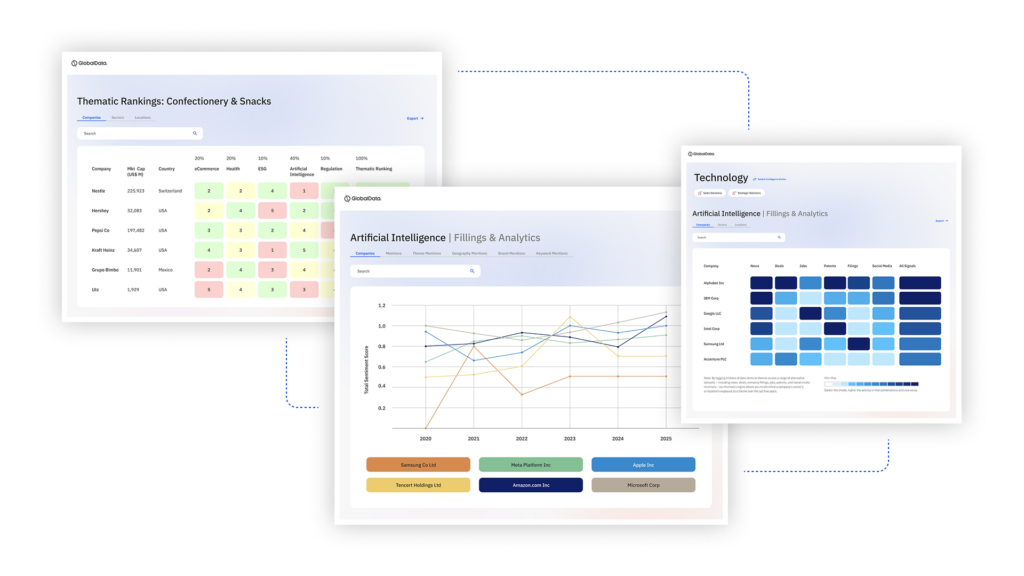
US Tariffs are shifting - will you react or anticipate?
Don’t let policy changes catch you off guard. Stay proactive with real-time data and expert analysis.
By GlobalDataThe US Food and Drug Administration (FDA) has provided Scholle IPN and Wright Foods with a letter of non-objection (LONO) for the initial installation of the new system.
Scholle IPN New Applications director Peter Messacar said: “Clearly consumers are continuing to demand this type of innovation as the spouted pouch format is so prevalent on store shelves today.
“As a decades-long leader in aseptic flexible packaging, customers have come to us to help them produce their freshest products possible.
“Separating the complexity and risk of pouch making from production operations affords our customers the ability to focus on what they do best. The CleanPouch Aseptic System is our answer to the market’s call.”