
Swiss carton packaging and filling machines supplier SIG has unveiled a new information management solution for filling line operations.
The new innovative service is designed to meet a growing demand for digital filling line solutions in the food and beverage industry. It delivers an accurate monitoring and information management solution using real-time data to optimise operations and improve productivity.
Known as combiLink, the new solution was developed to address the challenges associated with multiple reporting systems, obsolete data, manual data collection and a lack of filling line insights.
SIG’s combiLink connects filling line machines to collect data in customised reports outlining operational and technical efficiency. Customers can also track downtime incidents from their desktops, tablets or smartphones, which helps avoid bottlenecks and downtime.
SIG’s automation and digitalisation senior product manager Ayed Katrangi said: “56% of companies intend to increase efficiency by more than 20% over the next five years. combiLink can make a decisive contribution to this.
“It is a smart factory solution that offers a completely new way of monitoring and analysing the efficiency and productivity of a filling line, enabling customers to take on-time decisions fast and to automate operations to meet the needs of Industry 4.0, improve filling line overall equipment effectiveness (OEE) and optimises total cost of ownership (TCO), based on ISO 2240 standards.”
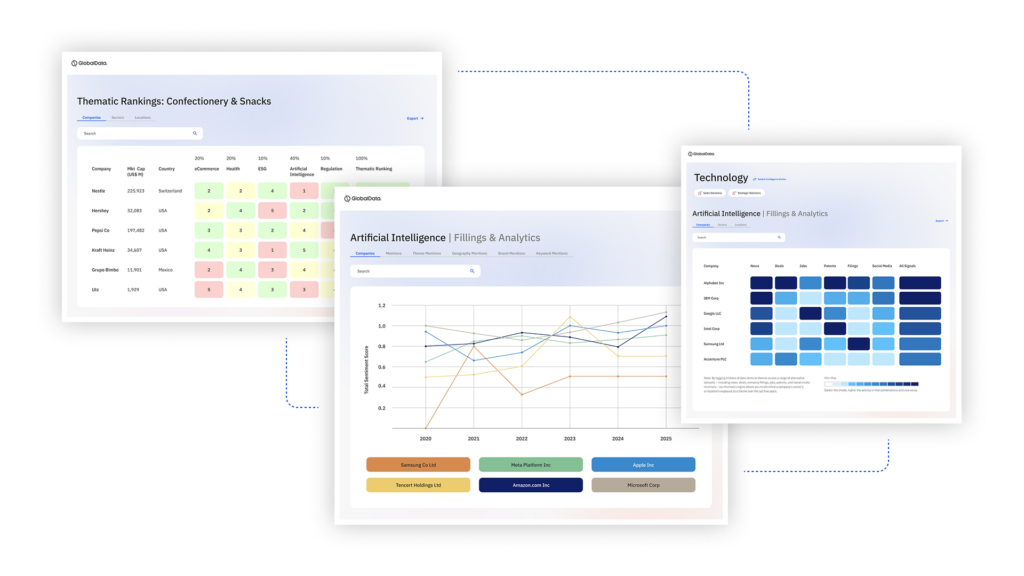
US Tariffs are shifting - will you react or anticipate?
Don’t let policy changes catch you off guard. Stay proactive with real-time data and expert analysis.
By GlobalDataConnecting machines in a filling line will enable producers to view current and historical levels of efficiency and performance, while also identifying future improvement areas.
combiLink can transmit data to business intelligence systems such as enterprise resource planning (ERP) and manufacturing execution systems (MES).
In addition, its open architecture and standards-based interface can be connected to Cloud-based systems and predictive analysis tools.