Canadian paper-based packaging solutions firm Supremex is planning to reduce its workforce in a move to enhance resource allocation and support its diversification strategy.
As part of the initiative, the company will cut a total of 41 jobs at its Canadian envelope operations, which accounts for 8% of Canadian envelope workforce.
The packaging solutions firm believes that the move will offer a reduction in operating expenses of around $2.7m annually. The company said that it will implement the reduction procedure in the current quarter and expects to complete it next year.
Supremex president and CEO Stewart Emerson said: “We regret the effect that these measures will have on employees and their families, and wherever possible, we have transitioned employees to our packaging business and worked with them on early retirement possibilities.
“These cost-cutting measures were necessary to improve operational efficiency and improve both competitiveness and profitability in our envelope business as we continue to prudently deploy resources into our packaging activities.”
Supremex offers envelopes and a range of paper-based packaging solutions to various customers, including resellers, government entities, SMEs and solutions providers across the US and Canada.
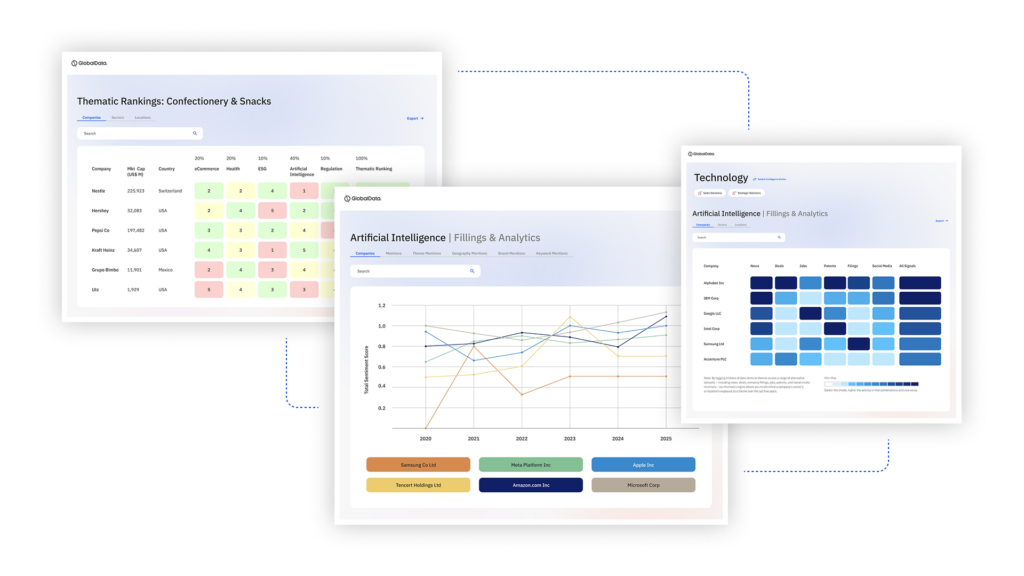
US Tariffs are shifting - will you react or anticipate?
Don’t let policy changes catch you off guard. Stay proactive with real-time data and expert analysis.
By GlobalDataThe company currently operates 12 facilities in Canada and three facilities in the US. It has approximately 830 employees across its operations.
Last month, the packaging firm reported revenue of $45.2m for the third quarter, which ended on 30 September 2018. A 4% increase year-over-year compared to $43.4m for the same period last year was also reported.
The company’s revenue from packaging and speciality products now account for 28.7% of sales, an increase from 21.6% in the third quarter of last year.