
Flexible packaging company Terinex Flexibles has officially opened its new EPC A+ rated factory in the UK.
The facility, located on Dove Valley Park near Derby, is claimed to be the UK’s first net zero CO2 rated building. It houses a flexographic printing operation.
The 46,000ft2 site is set to accommodate the company’s growth and innovation while prioritising sustainability.
Terinex Flexibles’ parent company OGM has invested more than £10m in the facility.
Designed by IMA Architects and developed by Clowes Developments UK, the new factory is more than twice the size of Terinex Flexibles’s previous factory in Ripley.
The building is equipped with the latest materials, machinery, technology, and processes, resulting in significantly reduced energy consumption and CO2 emissions.
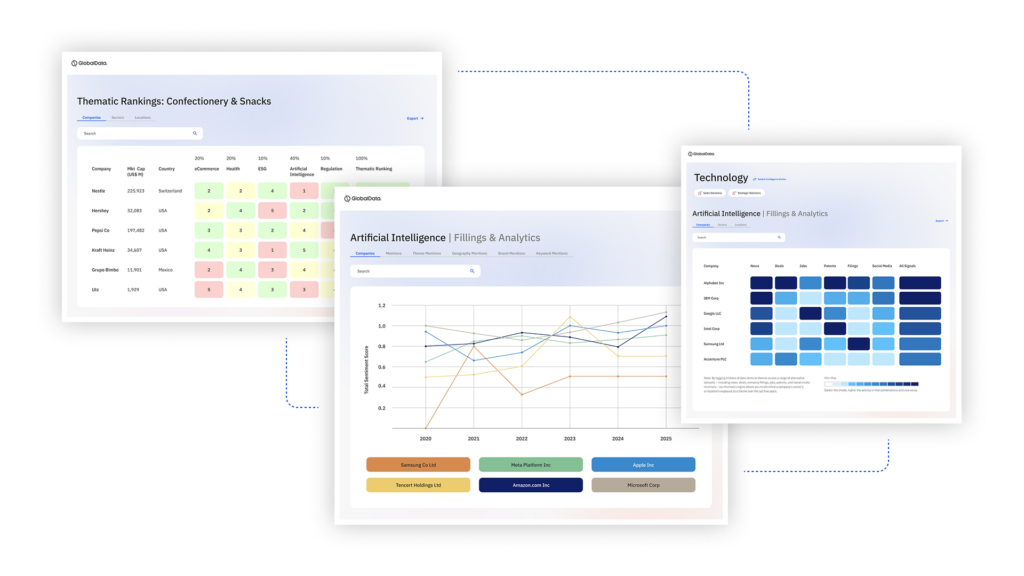
US Tariffs are shifting - will you react or anticipate?
Don’t let policy changes catch you off guard. Stay proactive with real-time data and expert analysis.
By GlobalDataIt is also capable of generating its own energy from renewable sources, with the potential for energy recovery and reuse for many years.
An innovative heat recovery system has been installed to capture energy from the byproducts of the printing process.
This system, linked to an advanced regenerative thermal oxidiser (RTO), is expected to generate between 45-230kW of energy, depending on the printing volume.
The captured energy is stored as hot water in two 10,000l buffer vessels and is used for drying ink and heating purposes, reducing the need for gas from the mains.
The factory’s roof boasts a 21kWp solar PV panel array, which powers the factory operations, including the 54kW immersion heaters in the buffer vessels.
OGM Holdings Group managing director Paul Wightman said: “We are proud to have created a state-of-the-art facility in terms of energy efficiency. As well as the fabric and services of the building, we are investing in efficient plant equipment and other energy-saving devices. For example, variable speed inverter drives have been added on all pumps and fan motors to further reduce consumption.”