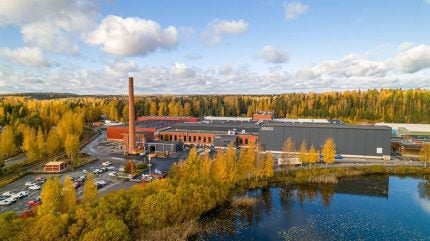
Pulp and paper technologies provider Valmet has agreed to supply its IQ Moisturizer system to Finland-based producer Adara Pakkaus.
Based in Valkeakoski, Adara Pakkaus manufactures corrugated board and packaging in the country.
The delivery will include an IQ Warp Control system and an IQ Moisturizer, which is said to be one of the most advanced moisturising systems in the industry.
Featuring air-atomised spray nozzles and linear water control valves, the system is designed to correct warping, reduce cracking, and optimise glue consumption.
The IQ Moisturizer will be integrated with the existing Valmet IQ Warp measurement for automatic control, aiming to reduce waste and improve both the quality of the corrugated board and the overall production efficiency.
This system expansion is part of Valmet’s IQ Quality Management Solutions, which focuses on monitoring and optimising process performance and end-product quality.
Adara managing director Teemu Salo said: “We have a very good cooperation with Valmet, and now we are upgrading the existing quality management system with an automatic profiler, aiming to reduce Edge-warp and S-warp that are impossible to be corrected with typical corrugator actuators even if they are well-maintained and in perfect condition.
“We believe that extended quality management solutions will help us to further improve and serve our customers even better.”
The order for the Valmet IQ Moisturizer system was recorded in the first quarter of 2024, with delivery expected in the third quarter of the same year.
The financial details of the transaction remain undisclosed.
Valmet Automation Systems business line technical sales manager Aki Leiniäinen said: “We have earlier supplied Adara with automatic moisture and temperature controls, utilising the Valmet IQ moisture measurement family to keep moisture levels in balance throughout the process.
“The IQ Moisturizer will be automatically controlled according to the existing Valmet IQ Warp Measurement, working in parallel with the existing Valmet quality management system in the production line.”