
Japanese company Asahi Kasei’s subsidiary Asahi Photoproducts has provided its CrystalCleanConnect automated flexo platemaking system to North American packaging company Winpak.
The new system has been installed at Winpak’s Films’ business unit in Senoia, Georgia, US.
Winpak has now become the first company in the US to install this CrystalCleanConnect system, Asahi noted.
CrystalCleanConnect, which was co-developed by Asahi Photoproducts, ESKO and Kongsberg, helps in preparing press-ready plates in a single step to further minimise operator’s interventions, unlike the traditional plate production method, which is a 12-step process.
It is said to be a user-friendly system that can easily be integrated into the existing printing processes, while addressing skill shortages by maintaining consistent print quality.
Winpak Films general manager Vishal Khushalani said: “We were looking for a more efficient and sustainable means of producing flexo plates, including the ability to bring platemaking in-house to reduce costs and lead times.”
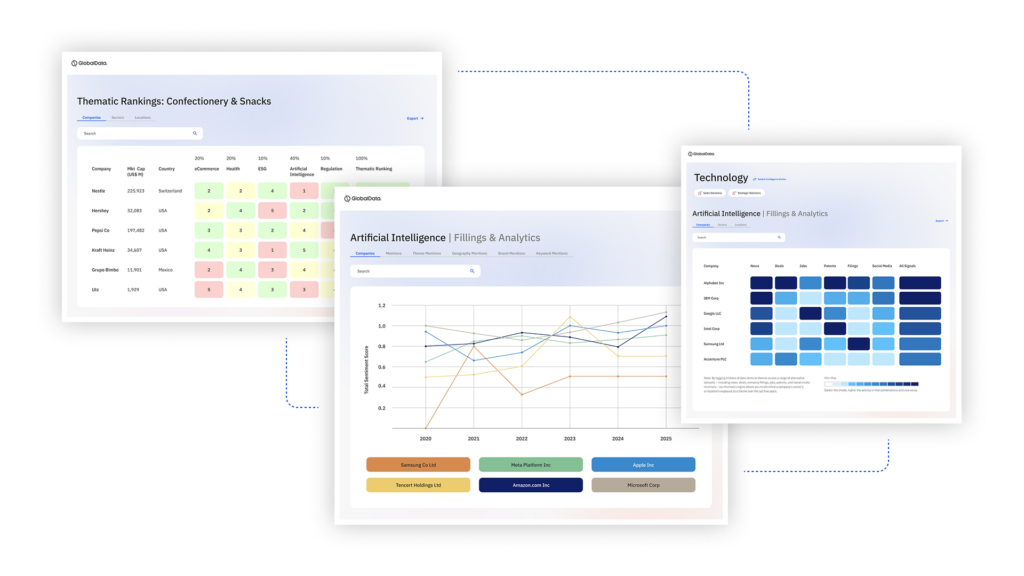
US Tariffs are shifting - will you react or anticipate?
Don’t let policy changes catch you off guard. Stay proactive with real-time data and expert analysis.
By GlobalDataWinpak specialises in the manufacturing and distribution of high-quality packaging materials and associated innovative packaging machines. It has a total of 12 production units in the US, Canada and Mexico.
The company’s products are primarily used for protecting perishable foods and beverages such as meat trays/covers and thermoformed cups and lids, as well as some healthcare packaging solutions.
According to Khushalani, earlier the company was outsourcing solvent-washed plates for manufacturing wide web flexible packaging and was looking to procure an in-house platemaking system, with ESKO plate imager, Asahi AWP water-washable plates and plate processor and Kongsberg’s cutting table all working as independent units.
By transitioning to this integrated platemaking process, Winpak aims to improve sustainability, minimise its waste, enhance cycle time and reduce dependency on skilled operators.
Khushalani added: “When we were outsourcing plates, in addition to [the] environmental impact of solvent wash plates, our customer lead times ran anywhere from one to two weeks.
“By bringing this initial platemaking configuration in-house, we were able to produce a plate every 45 minutes to an hour, so going from a week to an hour sounded amazing, and [the] solution lived up to its promise.”