
Non-ferrous pyrometallurgical plants across the globe rely on smelting furnaces to extract copper, nickel, lead, and zinc which are subsequently used in a wide variety of manufacturing processes. Renowned for their efficiency and speed, these assets need to be carefully maintained to operate at maximum capacity. Waste heat boilers (WHB) play a crucial role in recovering and utilising heat generated as a byproduct of these processes. However, these boilers are susceptible to high temperature sulfidation leading to waterwall degradation. This corrosive process has a detrimental impact on asset life and overall performance. This article will explore the causes of this type of corrosion and how it can be prevented.
What causes corrosion and erosion?
The flue gas stream within a smelting furnace WHB has huge dust content that may either slag on the surface depending on its melting point temperature or erode waterwalls. In general, metal oxides are present in the dust and are characterised as very erosive media.
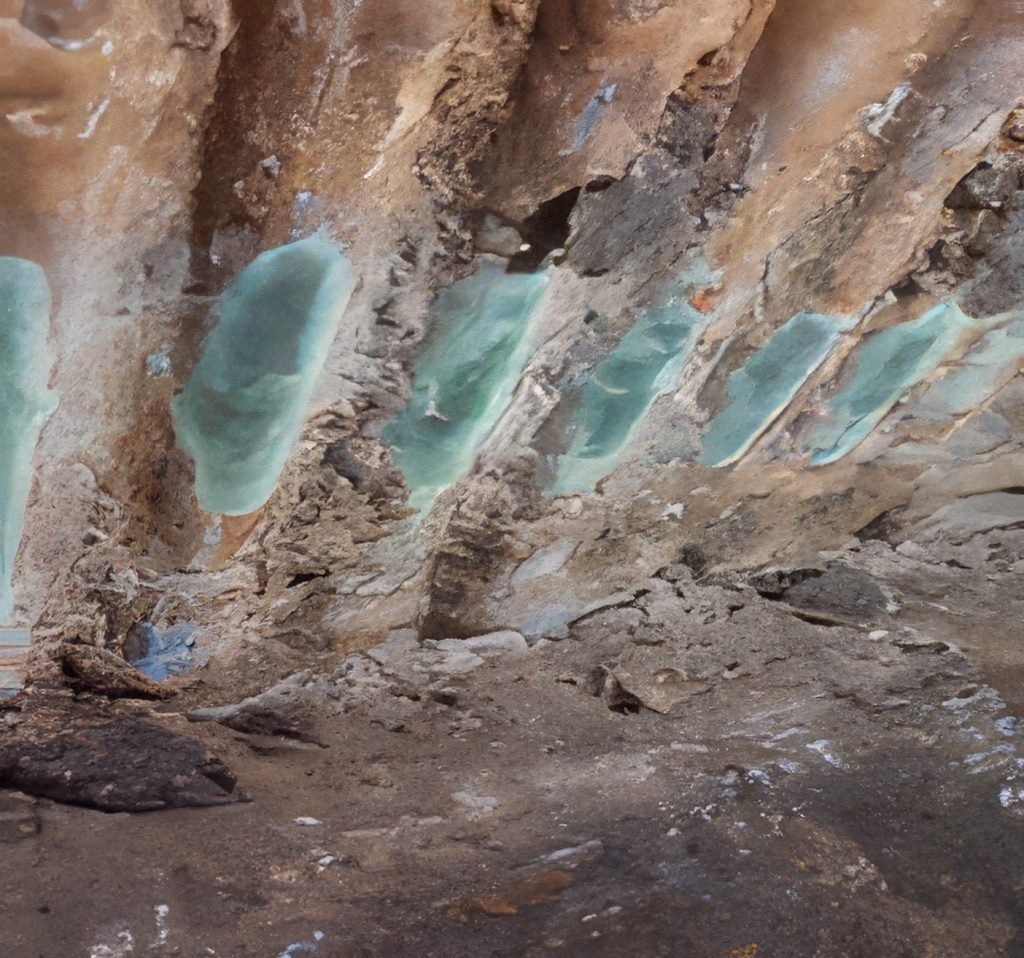
Flue gas originating from sulphur containing fuel becomes corrosive below a temperature of approximately 150°C (acid dew point corrosion). Local cold spots in metal air preheaters lead to rapid breakdown and corrosion of tubes and plates. This type of corrosion is one of the key factors negatively affecting the energy efficiency of waste heat boilers.
The incredibly high temperatures (which may reach around 1,350°C) circulating within the waste heat boiler start to affect the waterwalls. If this process is allowed to continue, areas of the boiler wall can become completely depleted and require costly shutdowns and urgent repair to operate efficiently.
Prevention methods: High Velocity Thermal Spray (HVTS)
High Velocity Thermal Spray (HVTS) by Integrated Global Services (IGS) offers a potential solution for extending the lifespan of existing smelting equipment by acting as an erosion barrier in critical apparatus.
Developed for safe on-site application, HVTS is a non-permeable thermal spray-applied alloy cladding material specifically designed for corrosion and erosion resistance in high-temperature smelting and mineral refining environments.
Engineered for the mining and mineral processing industry, HVTS ensures better bond strength and excellent corrosion and wear resistance. The solution is designed for fast on-site application, facilitating a prompt return to service. Its capability to withstand challenging environments makes it a suitable choice where other coatings may not provide lasting performance.
HVTS case study: WHB corrosion no longer a problem at copper smelter
In a collaborative initiative with a leading global copper smelting operation, IGS recently completed a project focused on improving the reliability and lifespan of a waste heat boiler. This case study highlights the technical implementation and explores the substantial commercial advantages realised by the copper smelter.
Traditionally, the copper smelter plant encountered significant challenges related to the waste heat boiler, with a service life of critical panels limited to only 11 to 18 months. This recurrent issue resulted in prolonged downtime, elevated replacement expenses, and logistical complications, further exacerbated by disruptions in the supply chain owing to the prevailing COVID-19 situation.
IGS addressed these challenges by introducing a high velocity thermal spray (HVTS) alloy cladding solution, aimed at extending the intervals between turnarounds. The successful implementation of this solution remarkably mitigated downtime and replacement costs.
The copper smelter plant in Chile, grappling with corrosion and erosion problems in their waste heat boiler, traditionally relied on panel replacements, single tube replacements, and weld build-up strategies. A pivotal moment arose when a representative of the plant discovered a waste heat boiler reliability project executed by IGS and approached the company in search of alternative solutions. Subsequently, a comprehensive technical presentation was made to the plant’s maintenance and commercial teams.
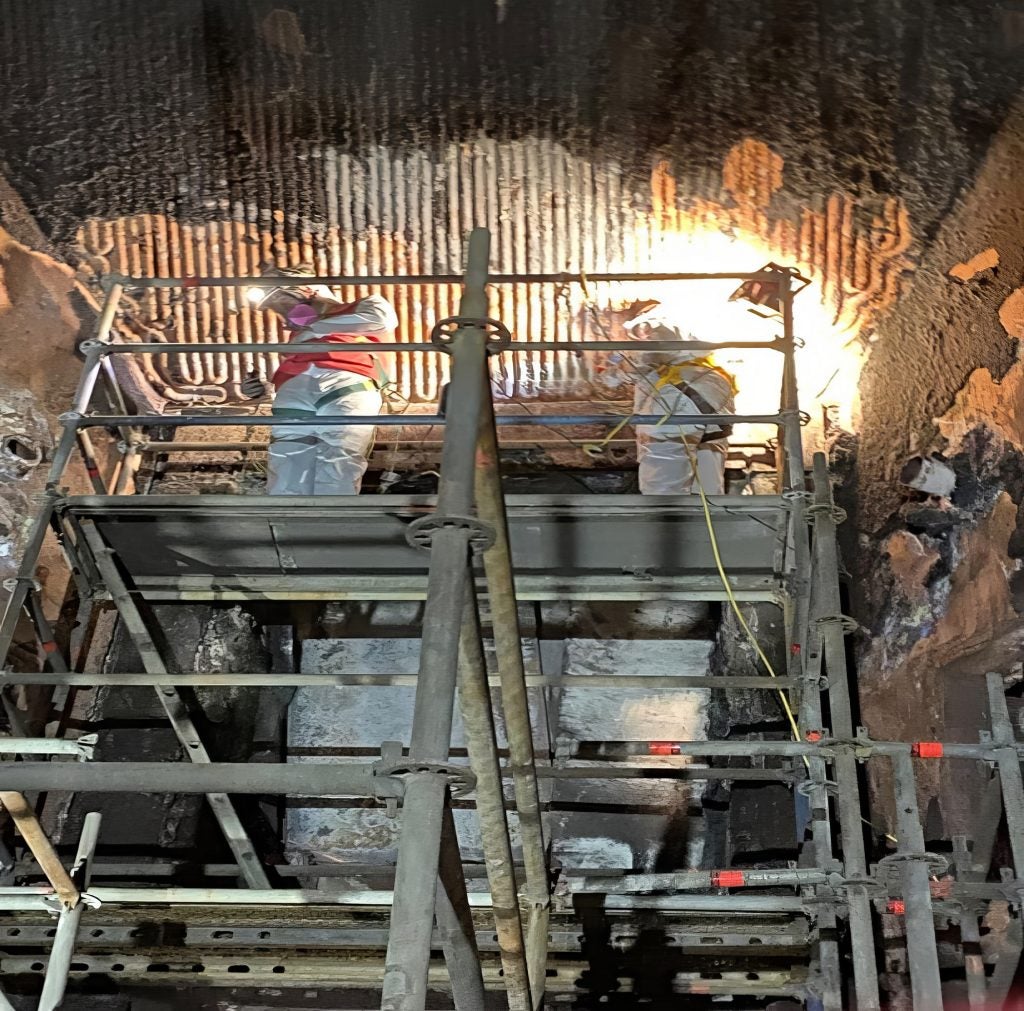
Following successful presentations and in-depth discussions, IGS secured a contract for the application of its proprietary HVTS high-nobility alloy cladding over a 70m2. The application took place in a laydown yard in October 2022, strategically targeting critical areas of the waste heat boiler.
The waste heat boiler operated continuously until the end of September 2023. In August, anticipating an outage, IGS mobilised an inspection crew, including local representatives from Chile. Despite a tight five-hour window, the team conducted a thorough inspection using magnetic lift-off (MLO) gauge testing. The results were overwhelmingly positive, with the cladding exhibiting no degradation after 11.5 months of service.
Kevin Phillips, overseeing both the project and inspection, described the cladding as being in an applied condition. “In all my years as a technical solutions partner, I have never had a client hug me. They were so pleased with the outcome!” remarked Kevin.
The success of the waste heat boiler project has opened avenues for potential collaborations on other critical components within the copper smelter. Converter hoods, copper cooling plates, and other identified assets are currently under consideration for IGS solutions. The client’s satisfaction has solidified IGS as a trusted partner.
Conclusion
The project addressing the waste heat boiler challenges demonstrates the company’s commitment to finding effective solutions. It has shown that a proactive approach and proven methods can contribute to overcoming operational challenges, potentially extending asset life and enhancing productivity. As the collaboration advances, the lessons learned from this project may inform future ventures, highlighting the potential for industry-wide advancements through strategic partnerships and innovative engineering approaches.
The examination of waste heat boiler challenges in copper smelters underscores the critical role these boilers play in the efficient extraction of metals. The corrosive effects of high temperature sulfidation pose significant threats to the operational longevity and overall performance of these crucial assets.
The collaborative efforts and successful outcomes detailed in the case study serve as a valuable reference for industries seeking reliable solutions to enhance the performance and reliability of waste heat boilers and other critical components in similar environments.