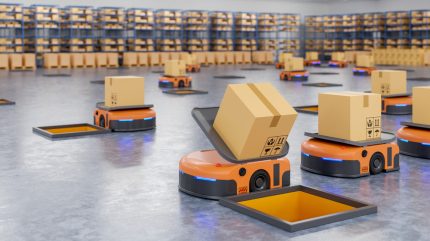
In today’s competitive landscape, packaging companies are under pressure to deliver speed, precision and cost control without compromising on quality.
From filling and labelling to palletising and logistics, automation is rapidly transforming every aspect of the packaging process.
By integrating smart technologies into production lines, firms are not only boosting efficiency but also future-proofing their operations against labour shortages, shifting regulations and rising demand.
Packaging lines powered by smart automation
Modern packaging plants are embracing automation to streamline repetitive tasks, reduce downtime and improve consistency.
Automated machinery—from robotic arms to vision systems—can now carry out complex sequences with minimal human intervention. This leads to faster changeovers, fewer errors and more reliable throughput.
In high-volume sectors like food and beverage, automated filling and sealing machines have become standard. These systems maintain strict hygiene standards while ensuring uniform output.
Meanwhile, in pharmaceuticals, track-and-trace technologies powered by automation help meet compliance requirements by providing end-to-end product visibility.
Robotic process automation (RPA) is also gaining ground in administrative areas such as inventory management, procurement and order processing. By automating back-office functions, packaging firms can significantly reduce delays and manual errors.
Many are seeing cost savings of up to 30% within the first year of implementation.
Crucially, automation doesn’t mean removing humans—it means allowing them to focus on tasks that require judgement, creativity or specialist knowledge.
Operators are now being trained to oversee automated lines, perform diagnostics and engage in continuous improvement initiatives, supported by real-time data.
Enhancing quality control and customer satisfaction
Automation is playing a vital role in ensuring product quality and improving customer outcomes. High-speed vision inspection systems can detect defects, misalignments or label inaccuracies in real time, rejecting faulty items before they reach the next stage.
This reduces waste, protects brand reputation and avoids costly recalls.
Smart sensors and Internet of Things (IoT) technology provide packaging teams with actionable data on machine performance, temperature, humidity and other environmental factors.
These insights enable predictive maintenance and ensure optimal storage conditions, especially in temperature-sensitive sectors like pharmaceuticals or perishable foods.
On the customer-facing side, automation allows for greater customisation. Digital printing, for instance, enables brands to run short, personalised packaging campaigns without retooling traditional lines.
This is especially useful in e-commerce and direct-to-consumer markets, where packaging now doubles as a brand experience.
Moreover, by automating data collection and compliance reporting, packaging firms can quickly adapt to customer requirements and industry standards. This responsiveness builds trust with clients and positions companies as reliable supply chain partners.
Preparing the workforce for automation in packaging
While the transition to automation offers substantial benefits, it also requires a shift in skills and workforce planning.
The packaging sector is already facing a skills gap, particularly in areas such as mechatronics, robotics programming and data analysis. As automation becomes more widespread, demand will grow for workers who can manage, maintain and optimise smart systems.
Forward-thinking companies are investing in training programmes to upskill existing staff and attract new talent. These include partnerships with technical colleges, apprenticeships and on-the-job learning that blends mechanical know-how with digital literacy.
Importantly, automation should be viewed not as a threat to jobs, but as a way to enhance workplace safety and job satisfaction. Repetitive, strenuous or hazardous tasks—such as heavy lifting or handling sharp tools—can now be assigned to machines, reducing the risk of injury and fatigue.
The packaging workforce of the future will be more diverse in skillset, with a focus on collaboration between humans and machines. As automation handles routine operations, people will play a central role in innovation, quality assurance and customer engagement.
Looking ahead
Automation and efficiency are redefining what’s possible in the packaging industry. From increased production speed and improved quality control to greater adaptability and customer satisfaction, smart systems are enabling packaging firms to meet today’s demands while preparing for tomorrow’s challenges.
As competition intensifies and sustainability pressures mount, the case for embracing automation has never been stronger.
Those who invest wisely—in both technology and people—will be best placed to lead the next generation of high-performance packaging operations.