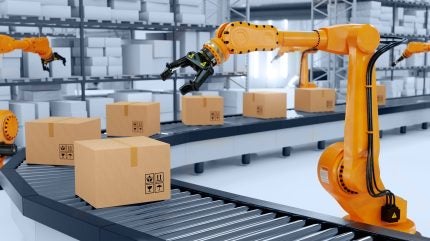
From robotic arms assembling boxes to autonomous systems sorting parcels at record speed, robotics is rapidly transforming packaging operations across industries.
As efficiency and precision become central to meeting rising demand, automated packaging systems are no longer a futuristic ambition—they are a practical necessity for manufacturers and logistics providers alike.
With global e-commerce growth and consumer expectations for faster deliveries, the packaging sector has become a critical bottleneck and a prime target for innovation.
Robotics technology offers a compelling solution by streamlining repetitive tasks, reducing error rates, and ensuring consistency across production lines.
Improving speed and accuracy in production lines
One of the clearest advantages of robotics in packaging is the dramatic increase in operational speed.
Robotic packaging systems, particularly pick-and-place robots, can process thousands of items per hour—far surpassing human capability in high-volume environments such as food, beverage, and pharmaceuticals.
These machines excel in tasks like case packing, carton erection, palletising, and product handling.
By integrating vision systems and sensors, robotic units can identify objects of various shapes and sizes, orient them correctly, and place them precisely into packages. This not only reduces material waste but also supports quality control by ensuring that every item meets strict packaging standards.
Accuracy is essential when dealing with fragile goods or regulated products. Robotic automation helps eliminate manual errors, ensuring consistency across every unit.
For example, in pharmaceutical packaging, robotic systems can count tablets, fill blister packs, and apply labels with micro-millimetre precision—safeguarding compliance with stringent health regulations.
Adapting to changing packaging formats and product demands
Flexibility is another key benefit robotics brings to packaging operations.
In the past, changing a packaging line to accommodate a new product type or format involved significant downtime and reconfiguration. Modern robotic packaging systems, however, are built for adaptability.
They can be reprogrammed to handle different packaging designs, sizes, and materials with minimal disruption.
This is particularly relevant in industries where packaging customisation is on the rise. For example, consumer demand for sustainable packaging has led to a shift from plastic to paper-based alternatives, requiring machines that can handle different physical properties.
Robotic arms equipped with adaptive grippers and AI-driven software can seamlessly adjust to new substrates and geometries, making it easier for companies to stay agile in a fast-moving market.
Retail trends such as personalisation and limited-run packaging are also driving demand for robots that can manage shorter production cycles and higher product variety.
Rather than relying on uniform batch production, packaging robots can now support on-demand workflows, helping brands meet consumer expectations without compromising efficiency.
Reducing costs and supporting labour challenges
While the upfront investment in robotic packaging equipment can be significant, the long-term cost benefits are substantial.
Automation reduces reliance on manual labour, which is particularly important as the sector continues to face workforce shortages and rising wages.
By reallocating human workers to higher-value roles—such as system supervision or quality assurance—businesses can make more strategic use of their teams while maintaining throughput.
Moreover, robotics contributes to operational continuity. In settings where absenteeism or seasonal labour fluctuations disrupt productivity, automated systems offer consistency.
During the Covid-19 pandemic, many packaging facilities that had already adopted robotics were able to maintain output levels despite reduced on-site staff.
Energy efficiency and resource optimisation are other areas where robotic packaging plays a role in cost control. Automated machines can be programmed to use only the exact amount of packaging material required, minimising waste and supporting sustainability targets. In palletising applications, robots can optimise load configurations to reduce transport volume and associated emissions.
Companies that invest in predictive maintenance systems for their robotic units further benefit from reduced downtime and repair costs.
Sensors can monitor wear and tear in real-time, alerting operators to potential issues before they lead to breakdowns—a critical advantage in high-speed, continuous operations.
Looking ahead
The integration of robotics in packaging operations is not merely a trend; it is a structural shift that is reshaping how goods are packed, handled, and shipped.
From increasing packaging line efficiency to enabling greater flexibility and cost savings, robotic systems are set to become an indispensable part of the modern supply chain.
As technologies such as machine learning, vision systems, and collaborative robots (cobots) continue to evolve, the packaging industry is poised to benefit from even greater levels of automation.
Businesses that embrace these innovations early are likely to gain a significant competitive edge, particularly in sectors where speed, accuracy, and adaptability define market success.
For packaging professionals navigating today’s complex demands, robotics offers a clear path to future-proofing operations—balancing productivity with sustainability, and precision with scalability.