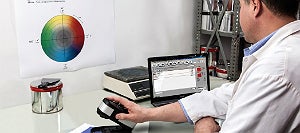
Because it takes considerable time and skill to mix these so-called waste inks for a new job, the containers may sit undisturbed for months, until management decides to clear stockroom shelves and throws them out. Losses from waste inks that are simply discarded can add up to hundreds of thousands of Euros for a medium-sized printing operation. Sometimes printing companies will recoup some value from the waste inks, by mixing them together to create a dark gray-brownish color that can replace the black component for black-toned colors, especially in the yellow- reddish spectrum. The mixed ink isn’t as valuable as its constituent inks, but at least some money is recovered.
Creating a profitable re-mix
But there is another option for printers to recoup much of their investments in inks, thanks to advances in color management technology. Using a spectrophotometer and new software from X-Rite Inc. geared specifically for ink formulations, one company was able to halve its stock of leftover inks in only a few months by remixing inks to fit specific new jobs, said Andrej Repar, technical advisor central Europe for Sun Chemical, the world’s largest producer of printing inks and pigments.
Leftover inks are a fact of life in the printing industry, Repar said, especially for companies that use large flexo and gravure presses that need to fill pipes, the ink chamber and pump sumps before a job is run. All of these voids in the press normally remain filled with ink even as the last sheet is run on the job. Most jobs may take ten to 15 kg of one ink to fill the press, but that can add up to 80 to 120 kg in leftover inks after each job for an eight-color flexo press.
The flexo printing trade has adopted routine ways to use waste inks simply because so much loss is at stake, but offset printers are showing interest in the reuse of waste inks because they more frequently use spot colors, even through their equipment typically doesn’t require as much ink as flexo or gravure presses.
Matching colors to make savings
Most printers label a waste ink with a sample sheet of the last job and store the container with the hopes that the company will get job requiring a similar color soon. If they find a similar color to existing leftover, printers add basic colors to try to match the color for new job. But matching color by eye with leftover inks takes considerable time and skill, with a result that is still unpredictable in volume, Repar said. The amount of re-matched ink can exceed the needed volume for job, possibly generating a larger volume of leftover. Or, if the volume of mixed leftover color is not enough for whole job, it’s difficult to reproduce the recipe.
InkFormulation’s recipe for success
Using the InkFormulation software from X-Rite Inc. and spectral data from leftover inks, a company can, in many cases, a create recipe of the target color that uses waste inks and new inks to achieve the desired color. "The economical impact of the InkFormulation software is significant," Repar said.
"It’s difficult to give a general estimate of savings because they are so dependent on print technology, consumption, and other factors. But it’s clear from what our customers tell us that the InkFormulation software reduces stock kept as leftovers and reduces press set-up time significantly."
Simple and user friendly for fast results
One of the highest hurdles to successfully implementing the use of waste inks is the company’s approach to color mixing and matching, Repar said. "Some managers believe that color mixing is simple, merely taking the spectral data and making up a recipe from instructions on a computer screen."
Even though the InkFormulation software is very user friendly and accurate, it still requires skill at mixing the inks properly. "Companies that put an experienced person who is familiar with computers in charge of an ink formulation program to save waste inks show a high degree of success in the shortest possible time."