
Automation has had a transformative impact on the packaging industry, marking a journey from humble hand-led tasks to the marvel of intricate machine operations. This profound shift, echoing through production lines and warehouses, charts a course from tactile precision to mechanical mastery.
Over time, automation brought about increased productivity and introduced a variety of innovative designs to the industry. Modern packaging now balances functionality with aesthetic appeal, guided by the advancements in robotics and smart design.
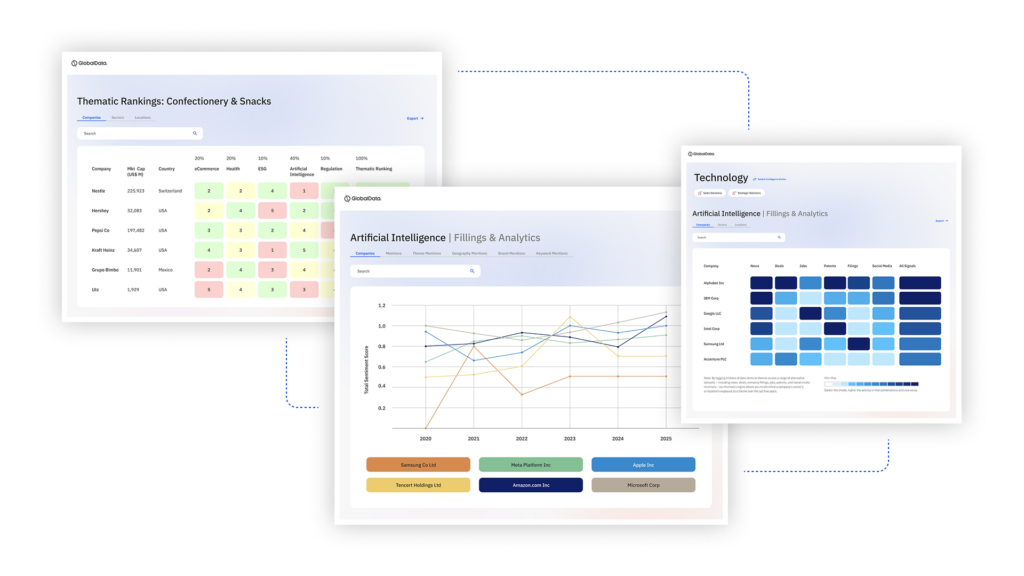
US Tariffs are shifting - will you react or anticipate?
Don’t let policy changes catch you off guard. Stay proactive with real-time data and expert analysis.
By GlobalDataCommon challenges in integrating automation solutions
Technical challenges
When businesses look to integrate new automated equipment, one of the first challenges they often encounter is compatibility with their existing software and machinery. Older equipment, designed before the rise of modern automation techniques, may not interface well with the latest systems.
Legacy systems, which can be in operation for years or even decades, come with their own set of integration challenges. Adapting these established systems to modern automation can be a complex process that requires detailed planning and expertise.
Financial challenges
Transitioning to automated systems often comes with a significant price tag. The initial costs of purchasing and integrating these systems can be a substantial financial burden, especially for smaller businesses or those operating on tight margins.
While automation promises increased efficiency and long-term cost savings, there’s often uncertainty surrounding the exact return on investment. Businesses may find it challenging to project the long-term financial benefits against the upfront costs.
Operational challenges
As businesses adopt new automated technologies, there’s a pressing need to train staff. Employees, accustomed to older methods and equipment, need to learn how to operate and maintain these new systems effectively.
During the shift to automation, maintaining product quality can be a concern. It’s essential to ensure that the changes in production methods don’t lead to inconsistencies or a drop in the quality of the final product.
Practical strategies to overcome these challenges
Comprehensive assessment and planning
Before implementing any new automation solutions, it’s crucial for businesses to assess their current operations. Identifying bottlenecks, inefficiencies, or outdated processes can help determine where automation can be most beneficial.
Having a clear vision of what a business aims to achieve with automation is essential. By setting specific goals and objectives, companies can ensure that their automation efforts are directed and purposeful.
Collaborating with experienced automation vendors
Choosing the right vendor can be a game-changer. Vendors with extensive experience in automation can offer valuable insights, advice, and solutions that can make the integration process smoother and more effective.
After the initial integration, having robust vendor support is crucial. Reliable post-implementation support can help address any issues that arise, offer updates, and ensure that the automated systems continue to operate efficiently.
Continuous training and skill development
With the rapid advancements in automation technologies, continuous training becomes essential. Investing in regular training programs ensures that employees remain skilled and confident in operating the latest systems.
The world of automation is always evolving. To remain competitive and effective, businesses must stay informed about the latest trends, technologies, and best practices in automation.
Real-world examples of successful automation integration
Case study — 1888 Mills:
After integrating modern automated systems, 1888 Mills experienced significant enhancements in its production process. Its journey into automation showcases the profound impact of technology when paired with strategic decision-making, leading to undeniable operational benefits.
Beyond mere technology adoption, 1888 Mills prioritised alignment with its broader business objectives. Through careful planning and a vision for the future, the company crafted an approach that not only addressed current challenges but also positioned it for long-term growth and adaptability.
Case study — Haley/Mitsubishi Electric:
When Haley and Mitsubishi Electric combined their expertise, the result was a tailored automation solution that addressed specific industry challenges. Faced with the ever-changing landscape of produce packaging, their collaborative effort yielded systems that were both adaptable and efficient.
The automation solutions developed by Haley and Mitsubishi Electric significantly enhanced the speed and precision of produce packaging processes, enabling them to handle a wide variety of products with minimal downtime. The integration of advanced robotics and intelligent software allowed for real-time adjustments to meet the dynamic demands of the market, ensuring both consistency and flexibility in their packaging lines.
Their story goes beyond the realm of technology, emphasising the importance of collaboration. Combining Haley’s deep insights into the product packaging domain with Mitsubishi Electric’s technical prowess, they crafted solutions that were greater than the sum of their parts. Through mutual respect and shared expertise, they unlocked new avenues of innovation and efficiency.
The future of automation in packaging
The next decade promises exciting advancements for automation in the packaging industry. Robotics, smart sensors, data analytics, and even specific applications of CMMS software are just a few innovations set to redefine how products are packaged and delivered.
Artificial intelligence (AI) and the Internet of Things (IoT) are at the forefront of the packaging transformation. While AI refines processes, predicts equipment needs, and personalises the packaging, IoT ensures a cohesive system where real-time data flows seamlessly across the packaging lifecycle.
Here are some other trends and developments likely to shape the sector in the upcoming years:
- Sustainable tech solutions: With growing global emphasis on sustainability, technology will play a crucial role in developing eco-friendly packaging solutions. Expect innovations that reduce plastic use, optimise materials, and incorporate biodegradable components.
- Personalised packaging: Advances in AI will facilitate more personalised packaging experiences. Brands can utilise data analytics to tailor package designs based on consumer preferences and purchasing behaviours.
- Smart packaging: IoT will revolutionise packaging with sensors that can provide real-time data. This might include information on product freshness, location tracking, or even user interaction data for marketers.
- Augmented reality (AR) in packaging: AR technology is set to make packaging interactive. Consumers might soon be able to scan packages with their smartphones to access additional product information, virtual user manuals, or interactive brand experiences.
- Blockchain for transparency: As supply chain transparency becomes vital, blockchain technology will be integrated into packaging processes. It will offer consumers clear traceability of product origins, processing, and transportation, ensuring authenticity and trust.
Addressing the challenges of automation is a strategic requirement for businesses eager to harness the full potential of modern technology. Confronting these issues directly allows companies to capitalise on the benefits while minimising disruptions and inefficiencies.
The road to a tech-driven packaging industry is clear, and automation sits at its core. Embracing this technological wave offers not just enhanced operational capabilities but also a competitive edge in the marketplace.
About the author: After an extensive career as a reliability and business improvement consultant, Eric joined L2L, where he currently serves as the Director of Smart Manufacturing. His role in this position is to help clients learn and implement L2L’s pragmatic and simple approach to corporate digital transformation.