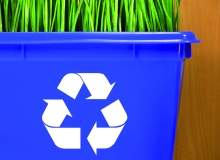
The central objective of food packaging is to preserve the quality and freshness of the product. Plastics and polymers fit the bill, but concerns about the volume of waste produced by such packaging, as well as the intensive use of hydrocarbons, are prompting companies to develop less environmentally damaging solutions.
Healthy-snack manufacturer Frito-Lay is one such eco-conscious brand, having developed a 100% compostable packaging solution for its multigrain SunChips snack product line. The bag material is constructed from more than 90% polylactic acid (PLA), derived from corn, and is designed to completely biodegrade in a compost bin under suitable conditions.
Since PLA is hydrophilic and absorbs moisture, Frito-Lay focused on developing a high-moisture barrier lamination film, applied between a metallic barrier layer and the PLA inner layer to protect the food from damage.
Produced in collaboration with four partner companies – Natureworks, SKC Films, Toray Plastics and Bryce – and in close consultation with customers, this material represents one of the first non-petroleum packaging products on the market.
Environmental breakdown
The development process hasn’t been without its teething problems – the original PLA bag was redesigned. Brad Rodgers, R&D manager of sustainable packaging and advanced materials research at Frito-Lay, explains that customer feedback played a significant role in this process.
See Also:
"There were a number of concerns raised about the noise, " he says. "Now, we took this to heart and my team spent the next six months back in the lab looking for ways to improve that design." Rodgers favours communicating directly with and updating customers by video via the company’s blog – a method that was used to address customer complaints and implement their ideas during the 2011 redesign.
How well do you really know your competitors?
Access the most comprehensive Company Profiles on the market, powered by GlobalData. Save hours of research. Gain competitive edge.

Thank you!
Your download email will arrive shortly
Not ready to buy yet? Download a free sample
We are confident about the unique quality of our Company Profiles. However, we want you to make the most beneficial decision for your business, so we offer a free sample that you can download by submitting the below form
By GlobalDataThe second bag, he says, provides all the protection of conventional plastic while also being "significantly quieter" and made from the same fully compostable PLA material.
"Through our testing, we found that by using different adhesives, which still meet our high performance standards, we were able to eliminate a certain amount of stiffness in the bag, which is what caused the crinkly noise," recalls Rodgers. "This adhesive layer acts a lot like a shock absorber between the two films, dissipating the sound waves that the polymers make. Think of the shocks on a car: they reduce the mechanical vibrations, and that makes for quite a ride when you drive down the road."
The new bag is designed to compost in under four months in a hot, active compost pile. "We have tested this and had a number of third parties validate our claims," assures Rodgers.
"You cannot simply dig a hole and put it in there; it won’t just go away. Composting generates heat as a by-product. The hotter the temperature, the faster it will break down. This bag will break down in 14 weeks at temperatures of 130°F. If your compost bin does not get that hot, that’s okay – it will still break down, but will just take a little longer."
Sustainable support
Developing the new polymer, however, is only the start; Rodgers suggests that using 33% PLA in the SunChips packaging structure is merely the first step in a bigger plan to launch such packaging in the marketplace on a large scale.
The next significant step is to identify a means to apply PLA in usable materials such as films. So far, only a select few converters and film manufacturers have achieved this feat and, of those suppliers, only a handful have successfully created and sold the resulting product at volume.
Rodgers says he is thankful to SKC for committing assets to support Frito-Lay’s efforts. The biopolymers field, he claims, is still in its infancy and the industry has a choice to either show its support or "throw rocks at the first truly commercial material available in an effort to shut it down before it really gets started".
It is his belief that "by supporting the biopolymers industry in purchasing significant quantities of this material, we are actually encouraging the whole industry to bring out their best efforts".
Green requirements
The Sustainable Packaging Coalition defines sustainable packaging as that which is safe and healthy for individuals and communities throughout its life cycle; satisfies market criteria for performance and cost; is sourced, manufactured, transported and recycled using renewable energy; and maximises the use of renewable or recycled materials.
The Coalition also stipulates that the material must be manufactured from components that are healthy in all probable end-of-life scenarios, using clean production technologies and best practices, and be physically designed to optimise materials and energy. It should also be effectively recovered and utilised in biological or industrial ‘cradle-to-cradle’ cycles.
Rodgers is largely in agreement with this, but concedes that it is not easy to cover all of these requirements at one time. He points out, for instance, that the material options for packaging managers are limited due to availability.
One can stumble upon the greatest material ever invented, but if it’s produced solely in the laboratory and it’s feasible only to create a handful of packages from it, then it can hardly be classed as sustainable. He recommends focusing on two or three areas to begin with, before building on this initial work.
According to Rodgers, there are many revolutionary, eco-friendly materials in the pipeline and the best way that large companies can support the further development and uptake of these materials is to identify ways of utilising them in their packaging.
"I am wholeheartedly engaged in finding as many ways as possible to use the right materials to achieve environmental improvements," he declares. "It just has to be backed up with scientific evidence, available in reasonable quantities and meet the performance expectations required to protect the product inside. Bring it on – I look forward to seeing these new materials develop into the commodity packaging that the whole industry needs."
This article was first published in our sister publication Packaging & Converting Intelligence.