
There’s a revolution brewing just over the horizon in the world of printing. New developments in conductive ink and nanotechnology are ushering in a new era of electronic printing that integrates new functions into printed surfaces themselves.
Although printed electronics have been used to develop lightweight displays, photovoltaic solar cells, flexible circuits and other technological innovations, the method has yet to make its mark in the packaging industry, a market offering dozens of applications for fully integrated electronic functionality, from aesthetic to practical and cost-saving.
Over the next few years, printed electronics look set to make inroads into the industry as the cost of the technology continues to drop and it starts to become a feasible option for a wider range of packaging concepts. Down the line, printed electronics have been indicated as a means for packagers to access futuristic ideas such as illuminated packaging, self-heating containers and inbuilt radio frequency identification (RFID).
Bringing printed electronics to packaging: the obstacles
As is the case in many industries, it appears that outsiders are leading the charge to bring printed electronics into the packaging space. One such outsider is NovaCentrix, a US-based technology company with expertise in nanomaterials, materials that exhibit special characteristics based on their nano-scale dimensions.
Initially, the company concentrated on developing printed electronics for markets such as photovoltaics and innovative display technologies. Although the potential applications of the technology for the packaging sector are obvious, material and financial hurdles have traditionally stood in the way of any major introduction of printed electronics to packaging.
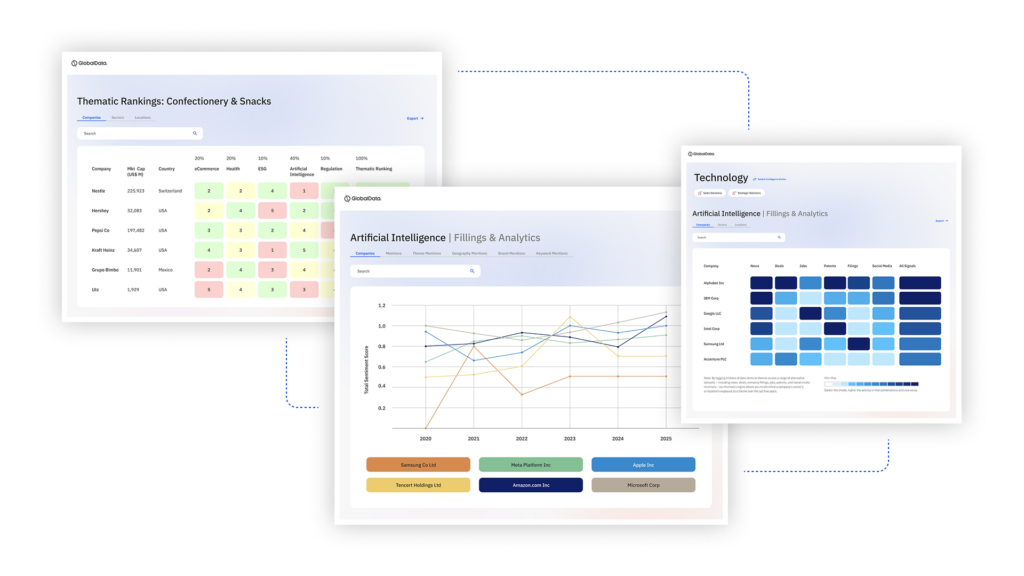
US Tariffs are shifting - will you react or anticipate?
Don’t let policy changes catch you off guard. Stay proactive with real-time data and expert analysis.
By GlobalDataOne such problem is that the intense heat-based processing required for conductive inks to be effective after they’ve been printed on to a surface (the additives that make conductive inks stable and printable have to be removed to restore the ink’s conductive properties) is simply too rigorous to be practical for most packagers.
"Broadly speaking, printed electronics are usually making use of flexible substrates like plastics, paper, cardboard and so on, and those materials are generally not able to accommodate the high temperatures that are typically needed to process these functional inks," says NovaCentrix’s vice president of marketing Stan Farnsworth.
A number of companies have been working on refining the ink chemistry to produce inks which are functional at lower temperatures, although Farnsworth believes the inherent cost of many of these techniques provides a similarly intimidating barrier of entry to packaging companies that aren’t developing ultra-premium concepts.
He was impressed by the innovation on show when he spent time at the recent drupa conference in Dusseldorf, but recognises that technical advances must always be matched by cost-effectiveness. "What’s driving that [innovation] is the constant push for improved graphics, for product packaging that stands out from competitors," he says.
"But of course, the concern is always cost, and so what kinds of cost numbers can be achieved while still having a differentiated product?"
Making printed electronics work
Related feature
Top trends in printing and ink for 2012
We profile the printers and inks that are transforming the packaging of tomorrow, both in quality and process efficiency.
Despite the formidable obstacles, NovaCentrix believes its research on nanomaterials, along with its PulseForge processing tools, has overcome them to the extent that printed electronics are now a viable and attractive possibility for the packaging world. At the core of the company’s solution is a process called photonic curing.
"What NovaCentrix has done is developed a new set of equipment that is able to heat the inks to the required processing temperatures, but without heating the substrates," explains Farnsworth. Overcoming the fundamental barrier of thermal incompatibility by separating the underlying packaging substrates has opened up the possibility for the technology to move forward in the packaging industry.
Although NovaCentrix is still looking for packaging partners to start implementing these new advances in real-life products, the company’s work using printed electronics to create integrated RFID, which is used to track products through the supply chain, has yielded some impressive results from a cost and efficiency perspective.
By replacing the materials traditionally used for RFID with cost-effective, copper-based conductive inks, Farnsworth believes printed electronics could reduce RFID costs by up to a factor of ten. This astonishing drop in price would partly stem from the ability to integrate RFID into a single high-speed printing line.
"Once we have some entry points [with packaging firms and RFID suppliers] established, I think it will move very quickly into no longer basing it on a traditional inlay where these devices are printed separately on a roll and then stuck on to a product," he says.
"The vision is to have these tags printed inline on a normal packaging line; they could potentially even be done digitally with inkjet, and then have a high-speed chip placement that’s inline as well."
Silver, copper and beyond: conductive inks
Related feature
Supporting eco-friendly packaging: green inks
Covering water-based and biodegradable inks and UV curing methods, Chris Lo finds out how the eco-friendly printing market is gradually turning ink green.
Reducing the cost of conductive inks has been a key goal for printed electronics developers who want to make this technology more widely available. Silver has traditionally been used as the basis for functional inks because of its high conductivity.
A great deal of research has been conducted to increase the efficiency of this metal, such as the development of particle-free silver ink by the University of Illinois, which has a lower processing temperature than standard silver ink and can be produced much more quickly.
However, the cost of the base material used for silver inks is an obvious impediment to progression of printed electronics in a cost-conscious, high-volume industry like packaging. "It’s certainly kept it from moving into packaging because packaging organisations just cannot be putting a bunch of silver on their cardboard boxes and making those economics work," says Farnsworth.
As a result, a number of potential alternatives are being researched, including an innovative new graphene ink (derived from pure graphite) developed by a research team at Cambridge University towards the end of 2011.
Copper, as a much cheaper and more abundant conductive metal than silver, has also been suggested, but until recently it was considered unfeasible because of the natural oxidisation process which it goes through, which often destroys the ink’s conductivity completely.
NovaCentrix is one of the companies that has revived interest in copper as a base material for conductive ink. Using photonic curing, the company has developed a way to start the process with ink based on copper oxide (oxidised copper, which Farnsworth describes as "a low-performing material but very, very inexpensive") and then convert it into copper once it has been printed.
"So we have a low-cost ink, and then it’s converted into copper with the processing tools on the cardboard after it’s been printed," Farnsworth explains. "At very high speeds, we can convert the ink to a very nice functional material that winds up being very low cost."
Inks and flexible packaging: the final hurdle?
An ink that starts as an ultra-cheap, useless substance but converts into a printed electronics system that almost matches the conductivity of silver-based inks sounds like the best of both worlds. However, that’s not to say it’s been easy to use it to develop efficient printed electronics – it’s not an easy process with any ink, especially when it needs to be printed on to packaging materials that vary so wildly in flexibility and molecular structure.
"You have all kinds of situations where if the ink is too brittle and the substrate flexes then the ink cracks, losing connectivity," says Farnsworth.
"Or if the ink flakes off, it just doesn’t stick – you can get a very good connectivity performance with the material, but as soon as there’s any distortion of the substrate then the ink flakes off, and that’s not going to do any good either."
Farnsworth acknowledges that there’s still a lot of work to be done and a lot of consultations to be made if printed electronics is going to gain a foothold in the packaging sector. "One of the points that we hope to learn from our initial foray into packaging is to understand what types of substrates and packaging opportunities are out there right now, and to see if we have a product set that can address those."
But with the technical and economic stumbling blocks that this technology has already overcome on its slow journey towards the packaging industry, there is no reason to doubt that, in time, it will cross the finish line. With the prospect of built-in solid state lighting, integrated tracking technologies and many more innovations that printed electronics have the potential to provide, there is a significant incentive for packaging companies to get involved at this early stage.
"Of course, we’re a long way from having an HD-quality image on a box of macaroni," Farnsworth says with a smile, "but there are a lot of steps that can happen before we get to that point."