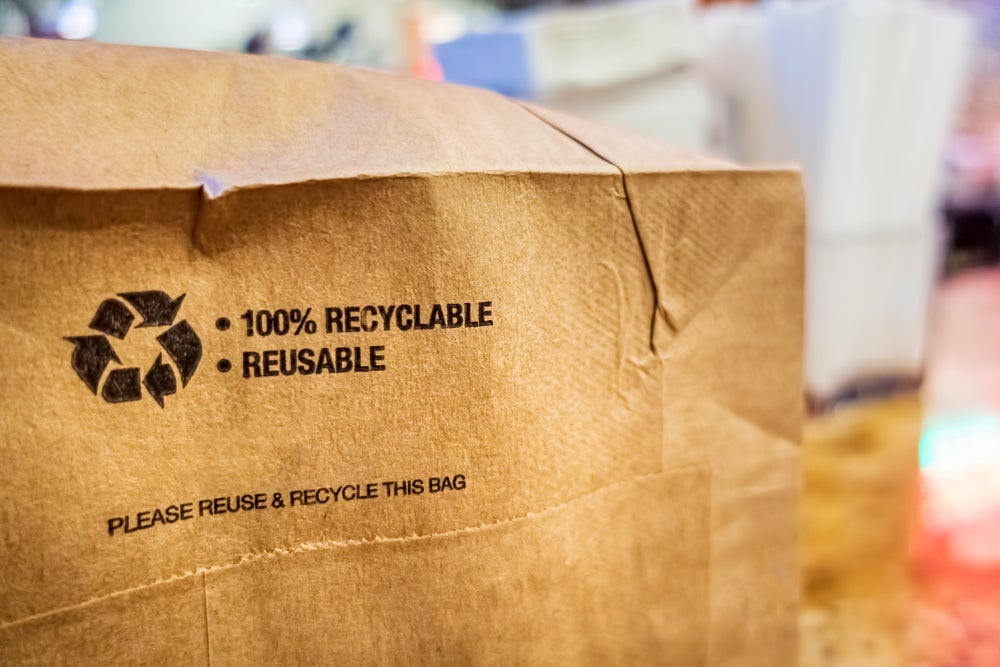
Industrial Physics, a US-based provider of packaging, product, and material testing, has unveiled insights into how professionals in the food packaging industry are responding to the growing demand for sustainability and consumer preference through innovative strategies for material selection and production processes.
In a comprehensive global survey encompassing various industries, including food and beverage, the research identified the primary drivers of packaging innovation among professionals.
Key drivers of packaging innovation identified
These drivers include:
- Quality assurance: A significant 69% of respondents highlighted the paramount importance of maintaining the quality of packaging.
- Product safety: Ensuring the safety and quality of the products contained within the package was a key concern, with 63% of respondents emphasising this aspect.
- Consumer-friendly design: Approximately 56% of professionals expressed the need for packaging to be user-friendly.
- Sustainability support: Nearly half, or 50%, of those surveyed were dedicated to supporting sustainability initiatives through their packaging efforts.
Toby Lane, Product and Applications Manager at Industrial Physics, noted: “Sustainability continues to drive material developments including plastic eradication from brands across the world. However, we must look at the broader picture in terms of material transportation weight, production energy, testing capability, food safety approval, and other related challenges.”
Investment in new materials amid cost challenges
Despite 60% of respondents grappling with rising material costs, the survey found a strong inclination towards investing in new material development.
Notably, 43% of professionals remain committed to reducing plastic usage, with biodegradable materials (58%) and organic alternatives (51%) emerging as the most promising avenues for exploring new packaging mediums.
Lane explained that the choice of materials should align with quality and safety requirements, as deviating from effective materials might inadvertently lead to increased food waste, contradicting waste reduction objectives.
Recyclability and waste reduction on the radar
The research also unveiled that packaging professionals in the food and beverage sector are actively investing in recyclability (60%) and waste reduction (59%).
Notably, 37% of respondents are exploring manufacturing processes like “lightweighting” to bolster waste reduction across the supply chain.
Lightweighting for efficient resource use
Lightweighting, which reduces the amount of material needed for metal packaging while maintaining durability, is a method gaining traction. Today, cans can be produced with a mere 0.097mm wall thickness, akin to a human hair.
This not only reduces production costs but also enhances resource efficiency.
Lane underscored the importance of maintaining durability and quality during the lightweighting process, highlighting the need to adhere to stringent regulations, including food-grade coatings, seam closures, and tamper-evident features.
Testing challenges in material and process development
Despite a strong overall inclination (96%) towards embracing new packaging developments, food and beverage professionals encounter challenges in testing new packaging types. Key obstacles include:
- High expertise costs: A substantial 63% of respondents cited the high cost of expertise as a barrier.
- Limited testing facilities: About half (50%) noted limited access to testing facilities.
- Lack of In-house expertise: A further 44% lamented the absence of in-house expertise.
Lane concluded by highlighting the ongoing relevance of testing equipment and methods. “Despite perceptions, the testing equipment and methods are still as applicable today. There are instances, for example in the case of recycled polymers where materials will behave differently and a new bank of data will need to be built, however, industry collaboration can prove valuable to gather a wider sample more quickly.
“Also, the equipment available today is often so automated that professionals do not need to have a highly specialised knowledge base to conduct the testing required,” he added.