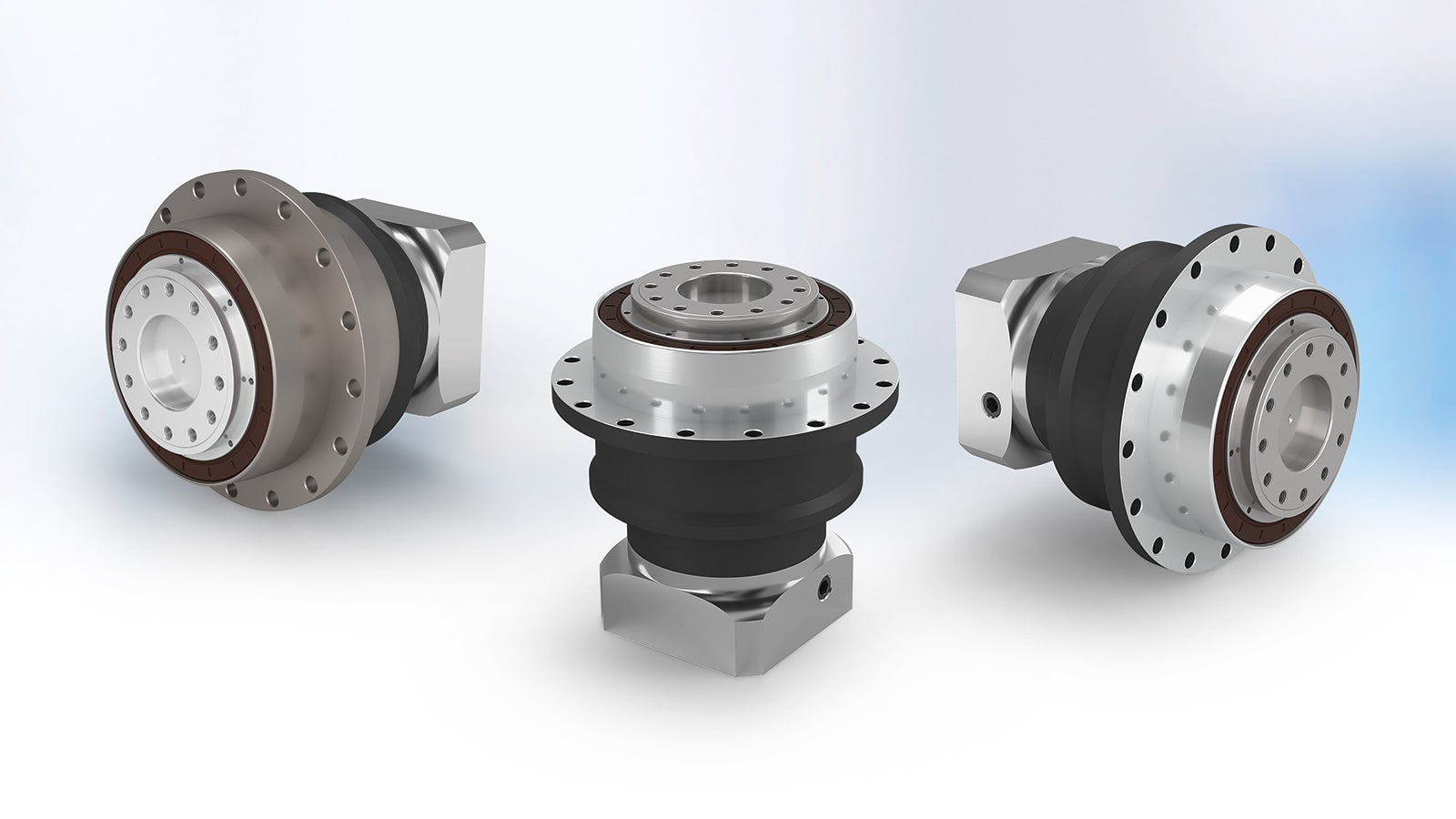
Application-specific solution for Delta robot drives
The gearbox specialist Neugart is expanding its range of application-specific solutions with a planetary gearbox specifically for Delta robot arm drives.
As a follow-up to the NGV, the planetary gearbox for industrial automated guided vehicles, and the hygienic HLAE, Neugart now presents the new NDF, another gearbox solution for a special field of application: It was developed specifically for use in Delta robots.
As parallel-arm robots with tripod kinematics, Delta robots offer very high dynamics and for this reason are used primarily for pick & place tasks, e.g. in automated packaging lines. They combine very fast movements with high positioning accuracy. This results in specific requirements for the servo motors of the main drives – and for the corresponding gearboxes. As a result, these gearboxes must meet the highest demands, especially in terms of inertia and stiffness, in order to ensure the necessary precision even at full speed.
Design details fulfil specific requirements
The Neugart NDF gearbox meets these special requirements with numerous technical details: For example, the gearbox enables extremely fast changes of direction thanks to a low-inertia clamping system at the input stage, which improves the dynamics and thus the cycle time of the robot. At the same time, the torsional backlash is limited to <1 arcmin as a standard feature. The gearbox with the frame size 090 operates with three specially designed planetary gears in the input stage and four in the output stage. This significantly increases the torsional stiffness and the transmittable torque. Four two-stage transmission ratios, each between i=22 and i=55, are available.
The output of the NDF has also received special attention in order to optimally meet the specific requirements of a Delta robot: The gear ratio at the output is i=5.5, which allows transmission of very high torques. The flanged output shaft with torque interface has 12 threaded holes (M8 instead of the usual M6), and the output flange has 16 holes (instead of the standard eight for each). The gearbox output shaft only rotates back and forth through a limited angle in Delta robots because of their design, making lubrication more difficult. An optimised radial shaft sealing ring in the NDF ensures optimum sealing of the shaft during rapid changes of direction.
A food-grade oil lubrication system is available as an option for the NDF. As an additional option, the NDF can be equipped with a stainless steel output shaft and a nickel-plated output flange. These options increase the corrosion resistance of the gearbox. As a result, it also tolerates frequent cleaning with aggressive media, which is essential in the food and pharmaceutical industries.