
In the constant sustainability battle fought between materials, glass offers promising eco-friendly potential but also major pitfalls.
While the material is infinitely recyclable and is popular among consumers, its key issues are the fossil fuel energy typically used in its production which contribute to significant carbon emissions.
Research by Queen’s University Belfast finds that the UK glass industry emits 1.7 million tonnes of CO₂ per year, with a further 0.5 million tonnes emitted in electricity production for use within the sector.
For packaging companies such as Ardagh, which manages immense glass production operations for international clients, the challenge of manufacturing glass sustainably and economically is crucial.
At a presentation in Ardagh Glass’s Doncaster facility in South Yorkshire, company representatives referred to carbon as the former “Achilles heel” of glass production but said that Ardagh “wants to be and will be a global supplier in sustainable packaging.”
There was a strong emphasis on the viability of sustainably using hydrogen, which the company feels is mainly thwarted by a lack of infrastructural support in the UK.
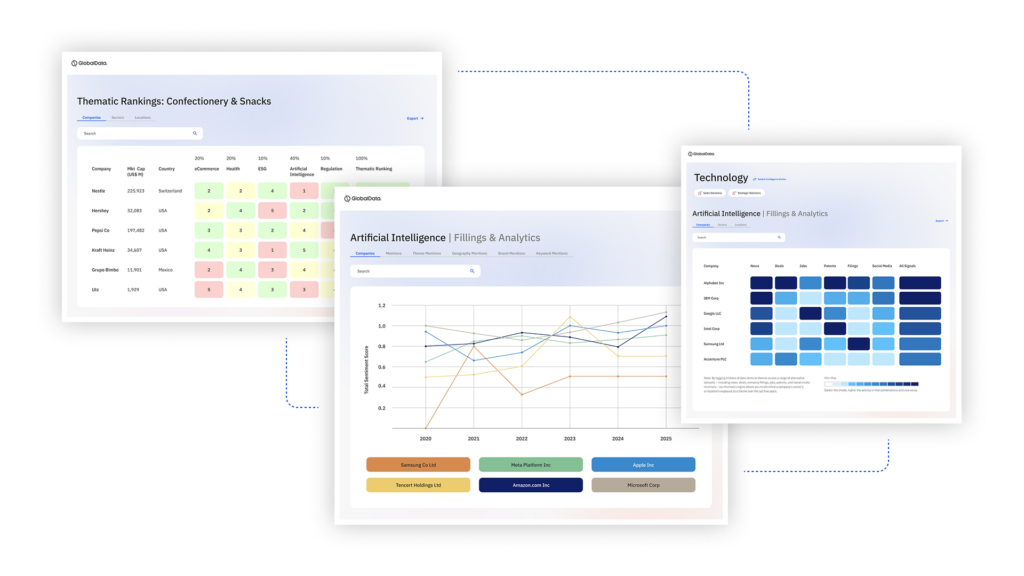
US Tariffs are shifting - will you react or anticipate?
Don’t let policy changes catch you off guard. Stay proactive with real-time data and expert analysis.
By GlobalDataSo, how is Ardagh Glass navigating decarbonisation within the business’s financial means?
Ardagh Glass’s manufacturing progress
Ardagh’s site in Doncaster, only one of its 56 facilities worldwide, is vast. At 172,000m² with three furnaces, it has glass manufacturing, sleeving, and print lines, alongside warehouse and recycling operations.
To make strides on sustainable glass production, Ardagh demolished a 20-year-old furnace in Doncaster and made a new investment at the start of 2023. With a more efficient melter, the new furnace is said to minimise carbon emissions and reduce gas consumption with a new investment in inspection technology. However, it is still fossil-fuel fired.
An upcoming development for the company is a Next-Gen furnace in its Obernkirchen facility in Germany, which is in its final stages. This will reportedly be powered by 80% renewable electricity and 20% gas, reducing CO₂ emissions by as much as 60% in the furnace.
Ardagh representatives confirmed that the Next-Gen furnace will be fed by a localised solar plant, supported by a €112.4m ($140.1m) grant from the German government.
Serving key clients such as Coca-Cola, Nestle and AB InBev, Ardagh made these upgrades after noticing that “Standards have gone up. They [our clients] drive us hard, but we’ve got to respond to these challenges to remain competitive.”
Across Ardagh’s European business, the company is pushing to hit emission and water reduction and renewable electricity targets from 2020 to 2030. But this is no easy feat.
The challenges of decarbonising glass
Ardagh UK business development director Dean Butler stressed that decarbonisation technologies for glass are not new and “have been options for us for many, many years. The difficulty is choosing when and where to deploy it and the scale required.
“The environmental impact of our business must be as low as possible but we’ve got to be economically sustainable. Decarbonising technologies are available, we could do it tomorrow with an infinite pot of money – which we don’t have. And that’s where we urgently need infrastructural support from the government.”
A key element of sustainable glass production is cullet, which is recycled broken or waste glass. Glass bottles and jars produced at Ardagh’s Doncaster site typically contain 50% cullet supplied through an independent, on-site recycling plant in Doncaster.
However, the main issue with sourcing cullet in the UK is that some of the glass collected in the UK is currently being exported, which Butler said “brings a tear to our eye” due to the subsequent missed sustainability benefits to domestic production and environmental issues.
At the core of the glass industry are melters, which are fired with natural gas and emit CO₂. Butler confirmed that fossil fuels can be replaced with hydrogen, which “can theoretically be used in any melter across the globe today. We could use hydrogen in our melters tomorrow. We just need access to it in a way that is commercially viable.”
Melters can also use electrodes to conduct electricity and replace some of the natural gas top fire, which could be useful for cutting-edge hybrid melters.
But as Butler pointed out: “Our plants are located where they are. The infrastructure that supports them to enable decarbonisation is lacking, especially in terms of electrical grid capacity.
“As our industry struggles to decarbonise, we’re talking about an industry killer.”
What is the UK government’s role in glass decarbonisation?
Decarbonising melters in the UK would require major government support. Electrical melters have sustainable potential but need large power generation facilities or electrical infrastructure.
In turn, upgrades to electrical infrastructure can take many years. Even if these are successful, for businesses such as Ardagh it would involve significant investment and could additionally be associated with high tariffs.
Butler stated that “on-site electrically generated hydrogen must be looked at as part of the wider solution to decarbonisation from the glass industry perspective.
“The other thing we know today is that the by-product of burning hydrogen is water, which will go into the combustion atmosphere in the furnaces. We don’t know the effects of that amount of moisture in the environment.”
Ardagh is part of alternative fuel trials but is once again limited by the high cost of biofuels. The UK government does not provide a fuel tax incentive for industrial applications. However, it does incentivise hydrogen business models where the difference in the natural gas to the hydrogen production is paid for.
The UK glass sector is reportedly discussing these issues with the government alongside other industries such as concrete, steel and paper.
Butler’s outlook on the glass industry’s future by 2045 is “high quality, high cullet, electric or hybrid furnaces and green hydrogen supply that is cost-effective. Timing is of the essence.”